Capping-machine Investment Guide for Cap Compression Machines
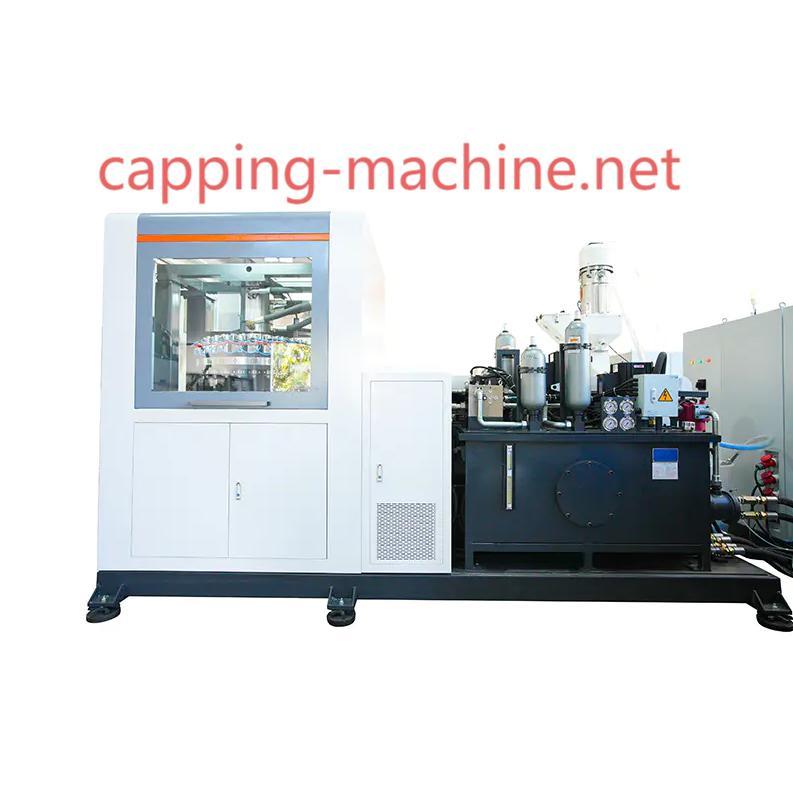
As production lines worldwide strive to meet rising demand for lightweight and efficient packaging, the Plastic Cap Compression Molding Machine has emerged as a vital tool in cap manufacturing. This system is particularly attractive to businesses that prioritize high-speed operation, reduced material waste, and consistent product quality. With these capabilities, Taizhou Chuangzhen Machinery Manufacturing continues to provide advanced compression molding solutions that support both volume and sustainability targets.
Unlike traditional injection molding, which uses high pressure to inject molten plastic into a mold cavity, compression molding simplifies the process by extruding a plastic pellet directly into an open mold. The mold then closes and compresses the material to form the cap. This results in less stress on the plastic, a more uniform wall thickness, and smoother finishes, which are critical factors for caps used in carbonated beverages, pharmaceutical bottles, and high-performance food containers.
One reason manufacturers increasingly invest in this equipment is the efficiency it offers in continuous production. Compression molding machines often operate with up to 48 cavities or more, delivering thousands of caps per hour. Since there is no need to cool injection runners or eject plastic sprues, the cycle time is significantly shorter. This design not only enhances throughput but also contributes to a cleaner and more compact factory floor layout.
Material savings is another clear benefit. Because the process requires only the precise amount of resin needed to form each cap, waste is nearly eliminated. Companies using this equipment report lower resin consumption per unit, especially when producing caps with complex features like tamper-evident bands or sealing rings. Taizhou Chuangzhen Machinery designs their systems to support HDPE and PP materials while minimizing thermal degradation, ensuring material efficiency without sacrificing cap performance.
Another key selling point is energy efficiency. Modern compression systems use servo-electric drives rather than traditional hydraulics, resulting in lower power draw and fewer fluid-related maintenance issues. In facilities running multiple shifts, these savings accumulate quickly. Chuangzhen’s machines are built with modular heating systems and precision cooling circuits that help stabilize temperatures and reduce energy fluctuations during long production cycles.
Cap quality is also more consistent when using compression molding. Because the plastic is compressed in a uniform cavity at controlled temperature and pressure, there’s less variation between caps. This consistency helps with capping machine compatibility, reduces torque deviation, and improves sealing reliability. For beverage companies especially, cap uniformity is crucial to maintaining carbonation integrity and shelf life.
Speed of customization further enhances the appeal. Many production lines need to shift between different cap sizes and shapes depending on seasonality or SKU demand. With Chuangzhen’s quick-change mold systems and adjustable control panels, these transitions can occur with minimal downtime. As a result, manufacturers can remain flexible and responsive to evolving consumer markets without investing in entirely separate production lines.
Moreover, the machines are often equipped with smart HMI interfaces and digital control systems, offering insights into operational parameters like torque settings, mold temperature, and output count. These tools allow supervisors to quickly adapt production conditions or diagnose potential issues before they lead to downtime. With Chuangzhen’s support, clients benefit from remote system access and tailored training to maximize machine utilization.
Maintenance considerations are minimal due to the simplified mechanical structure of compression systems. There are fewer internal moving parts, and most components are modular, allowing for fast replacement when necessary. Combined with regular technical support and quality-certified spare parts, Chuangzhen ensures production continuity for their clients.
For companies evaluating options in plastic cap manufacturing, Taizhou Chuangzhen Machinery Manufacturing offers highly efficient and customizable compression molding systems that integrate seamlessly with high-speed packaging operations. Learn more about technical features and factory configurations by visiting: https://www.capping-machine.net/ .
- Art
- Causes
- Crafts
- Dance
- Drinks
- Film
- Fitness
- Food
- Jocuri
- Gardening
- Health
- Home
- Literature
- Music
- Networking
- Alte
- Party
- Religion
- Shopping
- Sports
- Theater
- Wellness
