What Is Anodizing and How Does It Work?
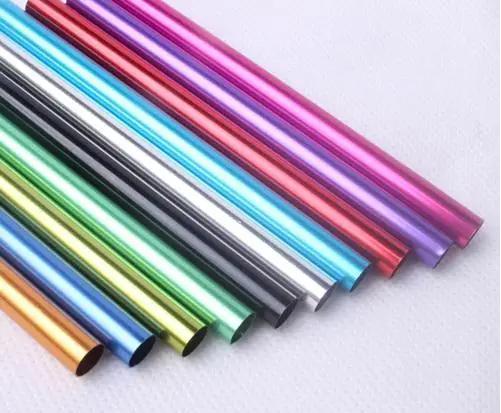
Anodizing is an electrochemical process that strengthens aluminum by thickening the natural oxide layer that already exists on its surface. This creates a much harder, more corrosion-resistant, and sometimes even more decorative surface. Anodising can involve up to five individual steps, though some may be combined depending on the application:
l Pre-Cleaning: The aluminum needs to be meticulously cleaned to remove any grease, oils, or contaminants that could interfere with the anodizing process. This is typically done with a hot alkaline or acidic detergent bath.
l Etching (Optional): A mild acid or caustic solution is used to etch the aluminum surface. This removes any minor imperfections and creates a uniform texture for a better final finish.
l Anodizing: The cleaned and (possibly) etched aluminum is submerged in an electrolyte bath, usually sulfuric acid. The part becomes the anode, and another electrode (the cathode) is placed in the tank. When the current is applied, oxygen reacts with the aluminum to form the oxide layer. The thickness of this layer can be controlled by factors like voltage, temperature, and anodizing time.
l Coloring (Optional): After anodizing, the oxide layer is transparent. Dyes or electrolytic coloring can be used to introduce various colors to the anodized aluminum.
l Sealing: The final step is sealing the porous oxide layer. This is typically done by boiling the aluminum in hot deionized water or a nickel-fluoride solution. Sealing strengthens the oxide layer and improves its corrosion resistance.
By understanding the process and benefits of anodizing, you can appreciate why it's such a valuable technique for enhancing the properties and aesthetics of aluminum. Maybe you are also interested in How Long Does Anodizing Last?
- Art
- Causes
- Crafts
- Dance
- Drinks
- Film
- Fitness
- Food
- Games
- Gardening
- Health
- Home
- Literature
- Music
- Networking
- Other
- Party
- Religion
- Shopping
- Sports
- Theater
- Wellness
