An Explanation Of The Fundamental Steps Involved In The Process Of Black Anodizing That Is Employed On Black Anodized Aluminum
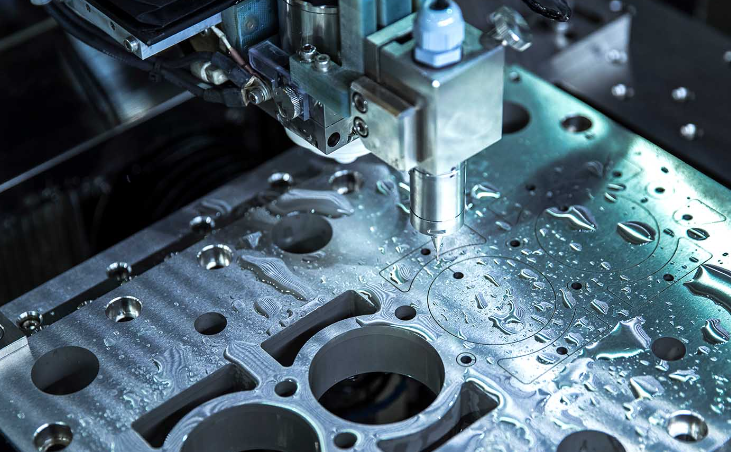
The coating not only lends the surface of the metal an aesthetic quality that is appealing to the eye, but it also makes the surface more resistant to wear and corrosion.
A type of electrolytic process known as black anodizing involves the darkening of a metal component, most frequently aluminum. Black Anodizing is most commonly used. The process of black Anodizing can be utilized on a wide range of different metals in addition to magnesium and titanium, which are both suitable candidates for the treatment.
an explanation of the fundamental ideas behind anodizing1. oxidation via anodization
After going through the process of being anodized in a bath that contains an acidic electrolyte, the aluminum will then be used as the anode in the battery. Once it has penetrated deeper into the pores of the aluminum, this oxide deposit will eventually cover the surface of the metal.
aluminum of series 6061 having a black anodization applied to it
2. Passing away or becoming extinct
3. The sealing procedure is carried out in a bath of acid or nickel acetate, which strengthens the coat so that it is less susceptible to wear and tear. This step is essential to the process as a whole.
The process of black Anodizing requires the following steps to be completed in order to be successful:Components and Various Useful Programs
The process of black Anodizing must first begin with a series of steps that are required because they are necessary for producing the desired results. These resources provide access to the following items as well:
a specific kind of electrolyte that is made up of sulfuric acid
Direct current that is supplied by a power supply that is completely saturated with color and employs direct current that is dye-colored
In order to properly store the electrolyte, an acid-proof container of some kind is required.
a look that is absolutely breathtakingly beautiful in its presentation
1. An aluminum surface that has been black anodized receives a stunning matte black surface finish, which qualifies it for use in applications relating to decoration and cosmetics
2. In addition to this, it gives the impression that a powder coating has been applied to the surface of it
3. It provides protection against the destruction that may be brought on by the presence of chemical compounds and high levels of humidity in harsh outdoor environments
4. This can occur when these conditions coexist
5. When the metal is treated with black anodizing, it stops corrosion from being able to damage the basic metal
6. It provides a better finish than powder coating while costing less than anodizing aluminum and offering better performance and aesthetics than powder coating does
7. This method uses dyes and tools that are a significant amount less expensive than those used in other methods
8. Aluminum that has been thermally stabilized, black anodized, and properly sealed is not only resistant to heat, but it also does not corrode and will not change its color
9. This is because the thermal stabilization prevents the aluminum from losing its original color
10. This is due to the fact that thermal stabilization stops the release of water vapor, which is the primary cause of corrosion
5. An Unparalleled Strength in Its Capability to Maintain Color
Components that have been black anodized have a fantastic capability of retaining their initial color even after being colored with inorganic or metallic salts. This is due to the fact that black anodization seals in the pigments that are used during the coloring process.
Aluminum that has been given a black anodized finish is used to make the limations.
After looking at the numerous benefits that black anodized aluminum components provide, the following are a few of the potential drawbacks that are associated with the utilization of this surface finish.
aluminum oxide in the black color that was made through the process of extrusion
1. An Attempt to Complete a Difficult Procedure Step
In order to achieve desirable results with anodizing, the aluminum must first be meticulously cleaned and subjected to pretreatment. After this step, careful management of the Anodizing and dyeing processes comes next, both of which are required for a successful anodization. Inadequate processing and protection also contribute to undesirable outcomes, most notably an uneven coating. To be more specific, this is the situation. a weakening in physical capacity
When something is exposed to the elements for an extended period of time, it will inevitably experience a certain amount of gradual fading over the course of that time. The reason for this is that organic dyes are unable to withstand the effects of being exposed to UV light in any capacity. This is the reason why this is the case.
When subjected to bright light, anodic coatings that are either insufficiently sealed or are extremely thin have a greater propensity to either lose their color or bleed. This occurs for a variety of reasons. In order to achieve the highest level of light-fastness that is physically possible, it is necessary to use high-quality dyes and adhere to a stringent sealing procedure. a broken or cracked appearance on the surface of the material
If the anodic coating is subjected to thermal cycling, there is a possibility that the coating will crack on the item that has been black-anodized. Because of this, there is a greater possibility that the coating will crack. It is common for the surface to have fissures in it because the substrate and the coating have different rates of thermal expansion. In addition, there is a restriction on the range of aluminum and aluminum alloys that can be processed using this method due to its restricted applicability. It is only compatible with the series 5, 6, and 7 of aluminum, with series 6 being the most common of those three series.
When compared side by side, a black oxide coating and a black Anodizing each have their own distinct characteristics and advantages.
The people who work in the manufacturing industry frequently argue with one another about which method, black Anodizing or black oxide coating, produces a better end product. This is one of the questions that is discussed frequently. It makes the surface of metals appear more appealing, reduces the amount of light reflection that takes place, and provides the metals with a moderate resistance to corrosion. The process of coating materials with black oxide is one that involves a chemical transformation, as opposed to the process of black anodizing, which involves oxidizing the metal.
On the other hand, black anodizing is a process that involves electrochemistry and helps to make aluminum more appealing and long-lasting than it would be otherwise. This is because it prevents the aluminum's surface from oxidizing. Before beginning the process of anodization, it is essential to confirm that all of the surfaces that are going to be treated are completely dry, clean, and free of any contaminants of any kind. This must be done in order to ensure that the anodization process will be successful.
- Art
- Causes
- Crafts
- Dance
- Drinks
- Film
- Fitness
- Food
- الألعاب
- Gardening
- Health
- الرئيسية
- Literature
- Music
- Networking
- أخرى
- Party
- Religion
- Shopping
- Sports
- Theater
- Wellness