Plastic CNC Machines: Precision Machining for Versatile Polymer Applications
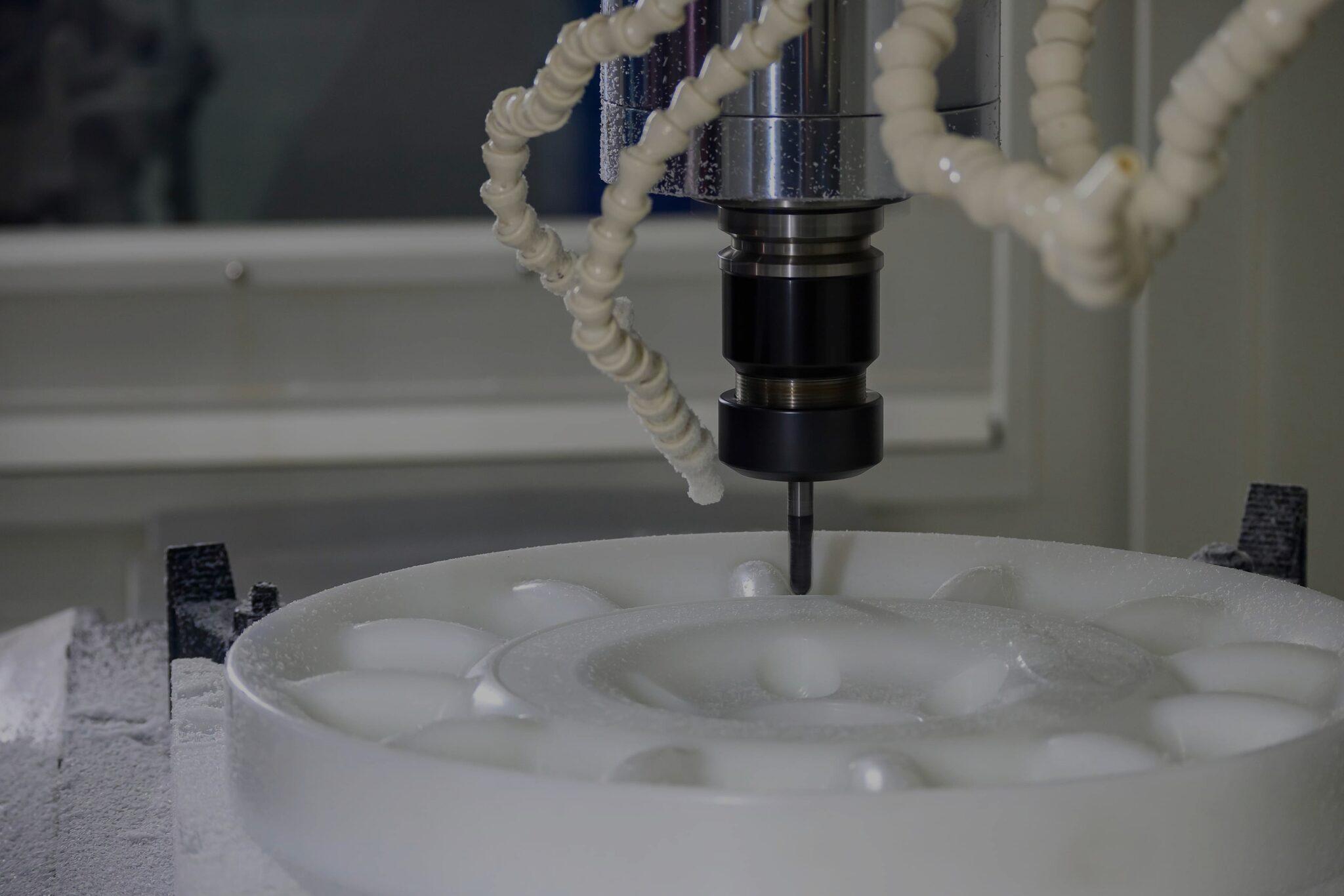
Plastic materials have taken a central role in manufacturing due to their versatility, light weight, resistance to corrosion, and cost-effectiveness. Whether in medical devices, consumer electronics, automotive components, or packaging, plastics are used everywhere. But shaping plastics with high precision and repeatability requires more than traditional tools—that’s where Plastic CNC Machines come into play.
CNC (Computer Numerical Control) machines specifically designed or optimized for plastic offer high-speed, high-accuracy machining, enabling manufacturers to create everything from prototypes to production-ready parts. In this article, we’ll explore how plastic CNC machines work, their advantages, common applications, materials used, and why they’re essential in modern production environments.
What Are Plastic CNC Machines?
A Plastic CNC Machine is a type of CNC milling, routing, or turning machine specifically used for machining plastic materials. While standard CNC machines can process metals and plastics, machines tailored for plastics are often configured with tools, speeds, and setups that are more suitable for soft materials.
These machines read digital design files (often created with CAD software) and translate them into precise tool paths using CAM software. The machine then cuts, drills, mills, or carves plastic parts with extreme accuracy, often within microns of the desired measurements.
Why Use CNC for Plastics?
Plastics might be easier to machine than metals, but that doesn’t mean precision isn’t important. CNC machines bring several benefits to plastic machining:
-
Tight Tolerances: CNC allows for consistent precision, especially important for assemblies and high-performance parts.
-
Surface Finish: Plastic CNC machining produces clean, smooth surfaces that often require minimal post-processing.
-
Speed and Efficiency: CNC operations are fast, automated, and suitable for both prototyping and production.
-
Low Tool Wear: Plastics are less abrasive than metals, so tools last longer, reducing maintenance and replacement costs.
-
Complex Geometry: CNC can handle intricate shapes, undercuts, and detailed engravings that manual tools can’t replicate.
Common Plastic Materials Used in CNC Machining
Not all plastics behave the same under cutting tools. Here are some of the most commonly CNC-machined plastics:
1. Acrylic (PMMA)
Used for clear display parts, lenses, and light diffusers. Known for its transparency and polishable surface.
2. Polycarbonate (PC)
Stronger than acrylic, with good impact resistance. Common in protective covers and enclosures.
3. Delrin (POM)
A durable engineering plastic with low friction, ideal for gears, bearings, and mechanical parts.
4. Nylon
Tough, flexible, and chemical resistant. Frequently used in automotive and industrial parts.
5. ABS
A lightweight, rigid plastic used in consumer electronics and automotive interiors.
6. PVC
Resistant to chemicals and moisture, often used in piping and medical applications.
7. PTFE (Teflon)
Non-stick and heat-resistant, often used in medical and aerospace components.
Different plastics require different cutting speeds, feeds, and tool types, which plastic CNC machines are configured to handle efficiently.
Types of Plastic CNC Machines
Depending on the part requirements and plastic type, different machines are used:
1. CNC Routers
Ideal for sheet plastics and sign-making, CNC routers are fast and good for large-format jobs. They’re used to cut acrylic sheets, PVC foam boards, and more.
2. CNC Milling Machines
Used for complex 3D shapes, holes, slots, and precision components. Milling machines are great for parts that require tight tolerances.
3. CNC Lathes
Best for cylindrical or rotational parts like bushings or spacers. Used for symmetrical plastic components.
4. CNC Laser Cutters
While not technically subtractive in the same way, laser CNC machines can cut and engrave plastics with high precision. Best suited for thinner materials.
Industries That Use Plastic CNC Machines
Plastic CNC machining is used across a wide range of sectors:
1. Medical and Healthcare
Plastic parts are essential in sterile environments. CNC machines produce:
-
Surgical trays and handles
-
Custom prosthetics
-
Medical housings
-
Dental components
2. Electronics and Consumer Products
From phone cases to laptop housings, CNC machines create:
-
Enclosures for circuit boards
-
Buttons and touchpad panels
-
Audio system components
3. Automotive
Interior plastic panels, clips, and covers are CNC-machined to fit precisely and look clean.
4. Aerospace
Weight-saving plastics are used for interior fittings and non-critical components.
5. Signage and Advertising
Acrylic signs, engraved plaques, and point-of-sale displays are often cut using CNC routers.
6. Prototyping and Startups
Early-stage product development often relies on plastic CNC machines for:
-
Prototyping
-
Model-making
-
Short-run production
CNC Machining vs. Injection Molding for Plastic Parts
While both processes are used to create plastic parts, each has its place:
Feature | CNC Machining | Injection Molding |
---|---|---|
Best for | Low-volume, complex parts | High-volume production |
Setup Cost | Low | High (due to mold making) |
Lead Time | Fast (hours to days) | Longer (days to weeks) |
Customization | Easy to adjust part design | Requires new mold |
Material Waste | Higher due to cutting | Lower after setup |
For many companies, CNC machining is the best way to develop and test plastic parts before committing to full-scale injection molding.
Best Practices for Plastic CNC Machining
To get the best results, here are a few things to consider:
-
Tool Selection: Use sharp, appropriate tools to avoid melting or chipping.
-
Speeds and Feeds: Plastic machining typically requires higher spindle speeds and lower feed rates than metals.
-
Material Clamping: Secure plastic parts gently to prevent warping or vibration.
-
Coolants: Avoid excessive coolant as some plastics react poorly to certain chemicals; air cooling or misting is often used.
-
Chip Removal: Use vacuum systems or air blasts to clear chips and prevent surface damage.
Advantages of Using Plastic CNC Machines
Here’s why more manufacturers are investing in CNC systems for plastic:
-
✅ Highly repeatable
-
✅ Ideal for low and medium volume production
-
✅ Supports rapid design changes
-
✅ Less setup time than molding or casting
-
✅ Works with a wide variety of plastics
-
✅ Supports both 2D and 3D machining tasks
As plastic technology evolves, CNC machines continue to adapt, opening new possibilities for complex and sustainable designs.
Conclusion: Shaping the Future with Plastic CNC Machines
Plastic CNC machines have become an essential part of the modern manufacturing world. Whether you're crafting a functional prototype, producing medical equipment, or shaping signage for retail, CNC technology provides the speed, accuracy, and flexibility needed to succeed.
As more industries seek efficient, scalable, and cost-effective production methods, CNC machining for plastics will remain at the forefront of innovation—bridging the gap between concept and creation.
- Art
- Causes
- Crafts
- Dance
- Drinks
- Film
- Fitness
- Food
- Juegos
- Gardening
- Health
- Inicio
- Literature
- Music
- Networking
- Otro
- Party
- Religion
- Shopping
- Sports
- Theater
- Wellness
