What are the Key Performance Characteristics of A Stamping Mould
Stamping is a widely used pressure processing method that involves applying pressure to materials at room temperature through a specially designed mould to achieve the desired shape of parts or semi-finished products. The performance of the stamping mould is of utmost importance as it directly influences the accuracy of the workpiece and the efficiency of the stamping process. Let's explore key performance characteristics of a stamping mold.
Wear Resistance: Wear resistance is a fundamental property of the mould material. During the metal stamping process, the material undergoes both flowing and sliding along the mould cavity's surface, leading to significant friction that can cause wear and eventual mould failure.
Hardness: The hardness of the material has a direct impact on the mould's service life and overall quality. A high level of hardness ensures prolonged durability and effective performance of the mould.
Strength and Toughness: To prevent sudden brittle fracture during operation, the mould must exhibit high strength and toughness. Strength indicates the material's ability to resist deformation and fracture, while toughness reflects its resistance to brittle fracture under the influence of strong impact loads.
Fatigue Fracture Properties: Good fatigue resistance is crucial for stamping moulds as they endure repeated loading conditions. Fatigue fractures can occur due to the cyclic stress experienced during the mould's working process.
High-Temperature Performance: Working at elevated temperatures can cause the hardness and strength of the mould material to decrease, resulting in early wear or plastic deformation.
Cold and Thermal Fatigue Resistance: Stamping moulds must demonstrate resistance to cold and thermal fatigue. The repeated heating and cooling cycles can induce tension, pressure, and variable stress, leading to surface cracking, increased friction, and reduced dimensional accuracy.
Corrosion Resistance: Some moulds, like plastic molds, may be exposed to corrosive gases during operation, which can erode the mould cavity's surface, causing wear and failure.
Geometric Parameters: The shape, fit clearance, and fillet radius of the die significantly influence the forming of stamped parts and affect the mould's wear and lifespan.
Good Process Performance: Forging performance and heat treatment performance are vital aspects of process performance. Forging performance refers to how the material behaves during the forging process, while heat treatment significantly affects the quality of the stamping mould, ensuring the desired hardness and wear resistance.
KENENG, as a reliable source manufacturer, can create customised stamping moulds according to your specific needs and carry out mass production. If you require assistance, do not hesitate to reach out to us. We are committed to providing high-quality and cost-effective services and products for all your stamping needs.
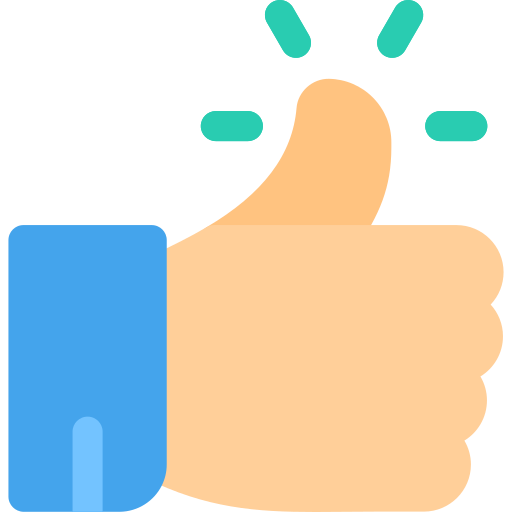
- Art
- Causes
- Crafts
- Dance
- Drinks
- Film
- Fitness
- Food
- Jeux
- Gardening
- Health
- Domicile
- Literature
- Music
- Networking
- Autre
- Party
- Religion
- Shopping
- Sports
- Theater
- Wellness
