How to Improve the Production Efficiency of CNC Milled Steel Parts?
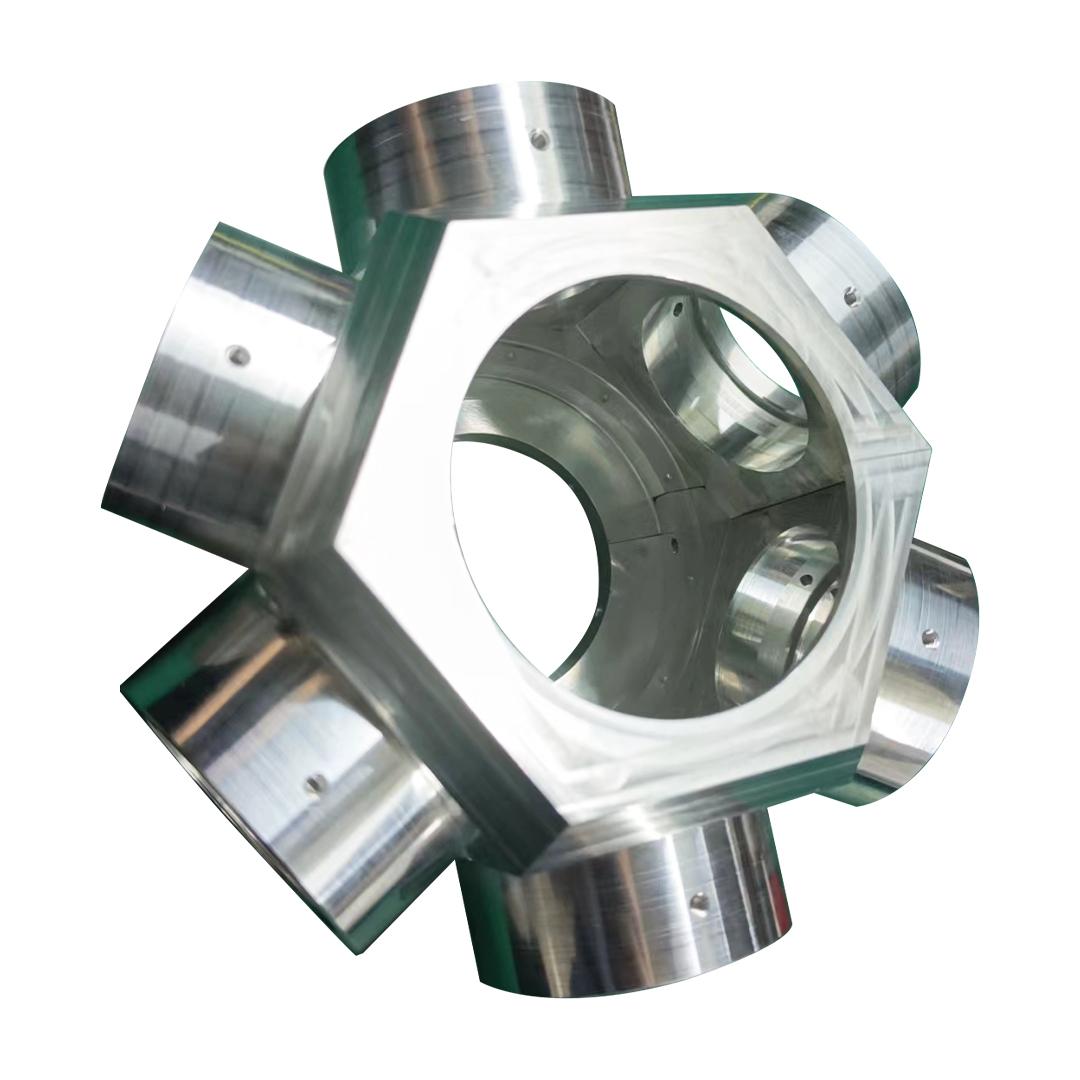
There are several strategies you can implement to boost production efficiency when CNC milling steel parts:
Optimizing Machining Processes
l Tool Selection: As discussed earlier, choosing the right tool for the job is crucial. Consider factors like material compatibility, geometry, and wear resistance. A well-suited tool will allow for faster cutting speeds and reduced tool changes, leading to increased production throughput.
l Cutting Parameters: Fine-tune cutting speeds, feed rates, and depth of cut based on the specific steel type and tool material. Optimize these parameters for efficiency while maintaining accuracy and tool life. Refer to manufacturer recommendations for starting points.
l Toolpath Strategies: Utilize efficient toolpath strategies in your CAM software. This includes minimizing toolpath length, avoiding sharp corners or sudden changes in direction, and employing techniques like trochoidal milling for faster material removal.
l Coolant Application: Employ a suitable coolant and ensure proper delivery to the cutting zone. This helps reduce friction, chip evacuation, and heat generation, leading to faster cutting and less downtime for tool changes.
Minimizing Setup and Idle Time
l Tooling Setup: Utilize quick-change tooling systems to minimize time spent on tool changes. Pre-setting tools offline can further reduce setup times.
l Workholding Techniques: Implement efficient workholding methods like fixturing or vises that allow for quick and secure workpiece loading and unloading.
l Machine Maintenance: Regularly maintain your CNC machine to minimize downtime due to breakdowns. Perform preventive maintenance tasks as per the manufacturer's recommendations.
l Production Planning: Plan production schedules efficiently to minimize machine idle time between jobs. This might involve batching similar parts together or utilizing nesting techniques to optimize material usage on the CNC bed.
Automation and Monitoring
l Automatic Tool Changers (ATCs): Invest in an automatic tool changer (ATC) if your production volume justifies it. This eliminates manual tool changes, significantly reducing downtime.
l In-Process Monitoring: Utilize in-process monitoring systems available on advanced CNC machines. These systems can track factors like cutting forces, spindle vibration, and tool wear, allowing for proactive adjustments and preventing tool failures.
Additional Considerations
l Machine Utilization: Strive for high machine utilization by keeping the CNC machine running productively during scheduled production hours.
l Operator Training: Invest in training for your CNC operators to ensure they understand efficient machining practices and proper tool handling techniques.
- Art
- Causes
- Crafts
- Dance
- Drinks
- Film
- Fitness
- Food
- Παιχνίδια
- Gardening
- Health
- Κεντρική Σελίδα
- Literature
- Music
- Networking
- άλλο
- Party
- Religion
- Shopping
- Sports
- Theater
- Wellness
