How Surface Treatment of 1060 Aluminum Circles Impacts Performance in Electrical Applications
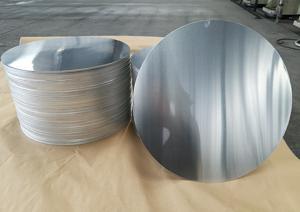
While 1060 aluminum circles are well-known in cookware and lighting, their application in electrical systems is equally important yet often overlooked. This blog delves into how surface treatment techniques—such as anodizing, chemical etching, and polishing—significantly enhance the performance of 1060 aluminum circles in electrical and electromagnetic applications.
Why Surface Treatment Matters
In electrical settings, the bare aluminum surface may oxidize quickly, reducing conductivity and increasing contact resistance. Surface treatments help stabilize and protect the aluminum circle while sometimes improving conductivity, corrosion resistance, and aesthetic value.
Anodizing for Dielectric Strength
Anodizing is a widely used surface treatment for 1060 aluminum circles, particularly when used as capacitor plates or in transformer windings. The anodized layer provides excellent dielectric insulation, essential for preventing short circuits and enhancing energy efficiency in electrical devices.
Chemical Etching for Better Bonding
Chemical etching roughens the surface at the microscopic level, allowing for better adhesion of conductive inks, adhesives, or lamination films. This is especially useful in printed electronics and flexible circuit boards where aluminum serves as a lightweight, low-cost substrate.
Polishing for Reflectivity in Infrared Devices
In electromagnetic and infrared applications, polished 1060 aluminum circles offer high reflectivity (up to 86%), making them ideal for use in infrared heating elements and reflective shielding. The smooth, mirror-like surface ensures efficient reflection and heat directionality.
Case Study: Busbar and EMI Shielding Applications
Some manufacturers employ 1060 aluminum circles in busbars due to their high electrical conductivity (~59% IACS). When paired with surface treatments, these circles resist corrosion and maintain performance over time. In EMI (electromagnetic interference) shielding, treated aluminum circles serve as lightweight, effective barriers against unwanted frequencies.
Customization and Thickness Control
For electrical applications, thickness tolerance is critical. Post-treatment circles must maintain dimensional stability, which is why controlled rolling and temper selection (e.g., O, H12, H14) are crucial for end-use performance.
Conclusion
Surface-treated 1060 aluminum circles are more than just raw materials—they're engineered components tailored for high-performance electrical applications. With proper treatment, these circles unlock new potentials in efficiency, safety, and reliability for a wide range of industries.
- Art
- Causes
- Crafts
- Dance
- Drinks
- Film
- Fitness
- Food
- Spiele
- Gardening
- Health
- Startseite
- Literature
- Musik
- Networking
- Andere
- Party
- Religion
- Shopping
- Sports
- Theater
- Wellness
