How a Pressure Control Factory Ensures Reliable Sealing Performance in Its Pressure Devices
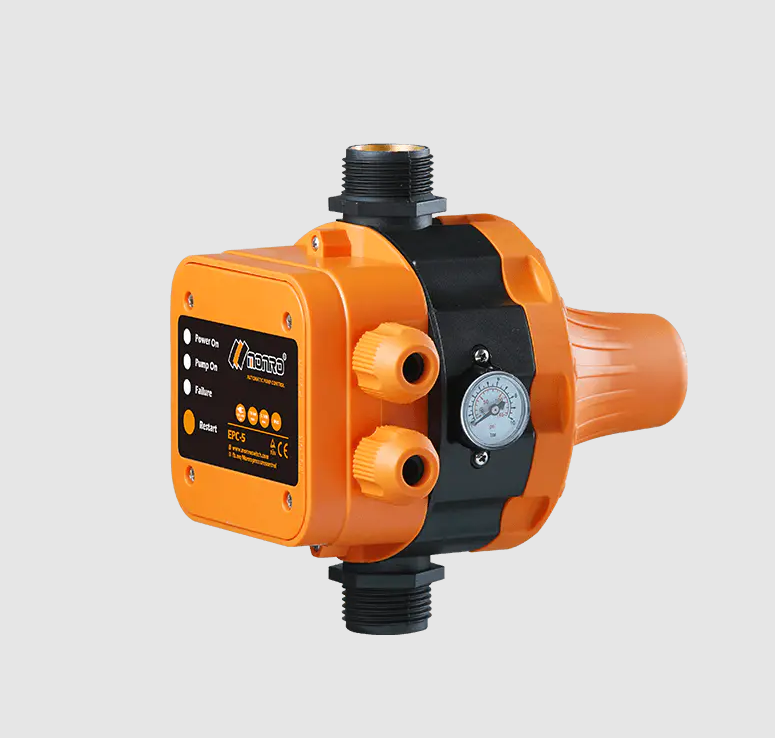
Sealing performance is a critical aspect of pressure control devices produced by a pressure control factory. Proper sealing ensures that the devices maintain their integrity under pressure, prevent leaks, and operate reliably in demanding environments. To guarantee high sealing performance, pressure control factories employ a combination of material selection, design innovation, manufacturing precision, and rigorous testing.
First and foremost, material choice plays a fundamental role in sealing effectiveness. Pressure control factories typically use advanced sealing materials such as nitrile rubber (NBR), fluorocarbon (FKM), silicone, or PTFE (Teflon) that offer excellent resistance to chemicals, temperature fluctuations, and wear. These materials provide flexibility and durability, forming tight seals that prevent fluid or gas leakage.
The design of sealing components also significantly impacts performance. Many devices incorporate multiple sealing layers or O-rings positioned strategically to enhance seal integrity. The geometry of sealing surfaces is engineered to maximize contact area and maintain consistent pressure across the seal, reducing the risk of gaps or deformation.
Manufacturing processes in a pressure control factory emphasize precision machining and assembly to achieve tight tolerances. Any imperfections or misalignments during production could compromise the seal, so quality control measures such as dimensional inspections and surface finish evaluations are essential. Automated assembly lines and computer-controlled equipment help maintain consistent quality.
Beyond materials and manufacturing, pressure control factories conduct extensive testing to validate sealing performance. Leak tests, pressure cycling, and environmental stress simulations assess how well seals perform under real-world conditions. Devices that pass these tests provide confidence in their long-term reliability.
In some cases, additional protective coatings or treatments are applied to sealing components to enhance resistance to corrosion, abrasion, or extreme temperatures. These measures further extend the lifespan of seals and improve overall device durability.
Furthermore, the factory may customize sealing solutions based on the specific application or medium involved. For instance, seals designed for corrosive chemicals differ from those intended for clean water or gases. This tailored approach ensures that each device operates optimally in its intended environment.
Finally, proper installation and maintenance are crucial to sustaining sealing performance over time. Pressure control factories often provide guidelines on how to handle and service their devices to prevent seal damage during use.
In conclusion, a pressure control factory guarantees sealing performance through careful selection of materials, meticulous design, precision manufacturing, thorough testing, and customized solutions. These efforts ensure that pressure control devices remain leak-free, safe, and efficient throughout their operational life.
- Art
- Causes
- Crafts
- Dance
- Drinks
- Film
- Fitness
- Food
- Jocuri
- Gardening
- Health
- Home
- Literature
- Music
- Networking
- Alte
- Party
- Religion
- Shopping
- Sports
- Theater
- Wellness
