Why Manufacturers Are Secretly Shifting to China Laser Welding Machine for Precision Welding Tasks
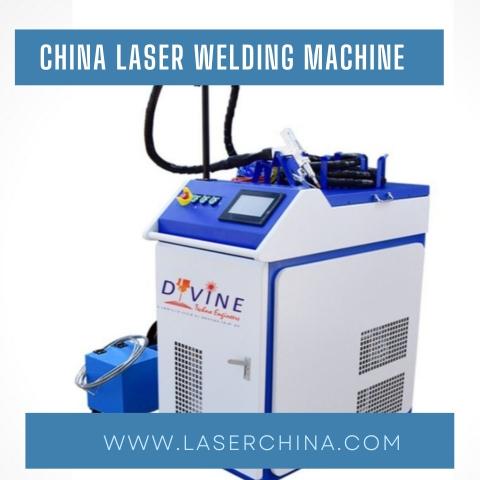
In the rapidly evolving world of industrial fabrication, where time, cost-efficiency, and precision define success, manufacturers are quietly but decisively turning their attention toward the China laser welding machine. This shift is not driven by marketing gimmicks or glossy brochures but by solid industrial performance that’s quietly disrupting traditional welding solutions.
Behind this growing trend lies a story of technological evolution, smart engineering, and strategic market placement. It’s not just about affordability anymore — it’s about matching and in many cases surpassing global standards in productivity and weld quality. So why are experienced metal fabricators, automotive assembly lines, and high-tech manufacturers adopting China’s laser welding machines as their new go-to solution?
Let’s uncover the reasons, the transformation, and what it means for global manufacturing standards.
Understanding the Rise of the China Laser Welding Machine
China’s manufacturing ecosystem has undergone a tectonic shift over the past decade. From being viewed merely as a mass producer of low-cost equipment, China is now at the forefront of precision engineering, especially in the field of laser technology. The China laser welding machine has become symbolic of this transformation — combining state-of-the-art fiber laser sources, intuitive control systems, and robust designs suitable for both small workshops and heavy-duty industrial settings.
These machines are no longer replicas or downgraded alternatives. They are the results of intensive R&D, partnerships with German and Japanese tech providers, and a deep understanding of global production needs.
What Makes the China Laser Welding Machine a Practical Choice?
The market isn’t shifting out of curiosity. It’s shifting because the machines deliver consistently. Whether you’re dealing with stainless steel, aluminum, carbon steel, or copper alloys, these machines are handling the job with minimal distortion, low heat-affected zones, and immaculate seam integrity.
One of the most interesting aspects is the growth of handheld fiber laser welding machines from Chinese manufacturers. These units are being adopted by metal gate fabricators, kitchen equipment suppliers, elevator panel manufacturers, and even in battery assembly plants. The speed and precision offered by a China laser welding machine is transforming workshop floors and increasing throughput without demanding massive capital investments.
The flexibility of integration with robotics, the accessibility of training resources, and the adaptability to different joint configurations have turned these machines into a preferred option across multiple industries.
Use Cases Proving Industrial Confidence
Let’s talk real-world usage.
1. Automotive Industry
OEM suppliers in countries like Turkey, Brazil, and India are integrating Chinese laser welding machines in their production lines to work on car doors, battery cases, and structural frames. Precision control allows for efficient joining of thin metals, which are common in lightweight vehicle parts.
2. Stainless Steel Furniture Manufacturing
From commercial kitchens to medical equipment, stainless steel is everywhere. Chinese-built laser welders are now standard in many workshops for clean, smooth joints that require little or no post-processing — a key factor in maintaining hygiene standards.
3. Aerospace Component Fabrication
Although stringent and high-precision, even aerospace subcontractors are incorporating China laser welding machines for secondary components like casings and support structures due to their consistency and compatibility with automation.
4. Battery and EV Assembly
The rise of electric vehicles and lithium battery production demands highly controlled welding environments. China’s technology in fiber laser welding, particularly in controlling heat spread and depth, is making it possible to weld battery tabs and casings without compromising cell integrity.
Why the Shift Isn’t Publicized Loudly
Interestingly, many large manufacturing entities don’t advertise their use of China laser welding machines. Why? It’s often due to internal sourcing policies, partnerships, or fear of backlash for moving away from traditional European or American machinery. However, behind closed factory doors, purchasing departments are negotiating with Chinese suppliers for bulk orders, maintenance packages, and localized tech support — all quietly transforming how welding is done at scale.
This discretion speaks to a strategic edge. While everyone’s focused on legacy equipment, those using China laser welding machines are optimizing cost per weld, reducing labor dependency, and scaling faster — all without making headlines.
Key Players Driving the Revolution
Several manufacturers from China are leading the charge:
-
Hymson Laser: Known for high-speed laser welding systems used in auto and electronics.
-
Raycus Laser: Offers powerful fiber laser sources integrated into OEM welding machines.
-
Maxphotonics: A critical player in fiber module development, enabling portable and handheld devices.
-
Han’s Laser: One of the most globally recognized Chinese laser brands with advanced automation lines.
These companies not only offer machinery but also provide industrial integration services, spare parts logistics, and training modules tailored to international buyers — especially in Europe, Southeast Asia, and the Middle East.
Affordability Meets Performance
While cost is a major draw, it’s not the only factor. A China laser welding machine often comes at half the price of a Western counterpart but delivers results within 90–95% of the benchmarked performance in most use cases. In industries where margins are thin and delivery timelines are tight, that 5–10% trade-off (if any) is more than acceptable when paired with reduced capital expenditure and quicker ROI.
But it's not about cutting corners — it’s about expanding access. Small and medium enterprises that previously couldn’t afford laser welding tech are now running three shifts a day with handheld models from Chinese suppliers.
Training, Maintenance, and Support
One of the biggest concerns foreign buyers had in the past was lack of support. Today, that issue is fading. Chinese manufacturers now offer multi-language manuals, remote diagnostics, online operator training, and 24/7 support channels.
Additionally, many local distributors and third-party service companies have partnered with Chinese manufacturers, especially in regions like UAE, India, and Eastern Europe. Spare parts availability is no longer a major bottleneck, and machine uptime is rivaling legacy brands.
Final Thoughts
The industrial landscape is changing, and the China laser welding machine is at the forefront of this transformation. It’s no longer about where the machine is made — it’s about what it can do. With proven reliability, precision output, and affordability, this equipment is leveling the playing field.
Forward-looking manufacturers understand that innovation isn’t just about new products — it’s about smarter production processes. The quiet shift toward Chinese laser welding machines reveals a deeper trend: the industrial world is moving toward accessibility, flexibility, and rapid adaptability.
Whether you're a fabrication shop owner, a production line manager, or an industrial investor, ignoring the capabilities of the China laser welding machine means potentially missing out on a powerful tool in your growth arsenal.
- Art
- Causes
- Crafts
- Dance
- Drinks
- Film
- Fitness
- Food
- Juegos
- Gardening
- Health
- Inicio
- Literature
- Music
- Networking
- Otro
- Party
- Religion
- Shopping
- Sports
- Theater
- Wellness
