Ensuring Cutting Accuracy in Hydraulic Angle Steel Cutters Through Design and Maintenance
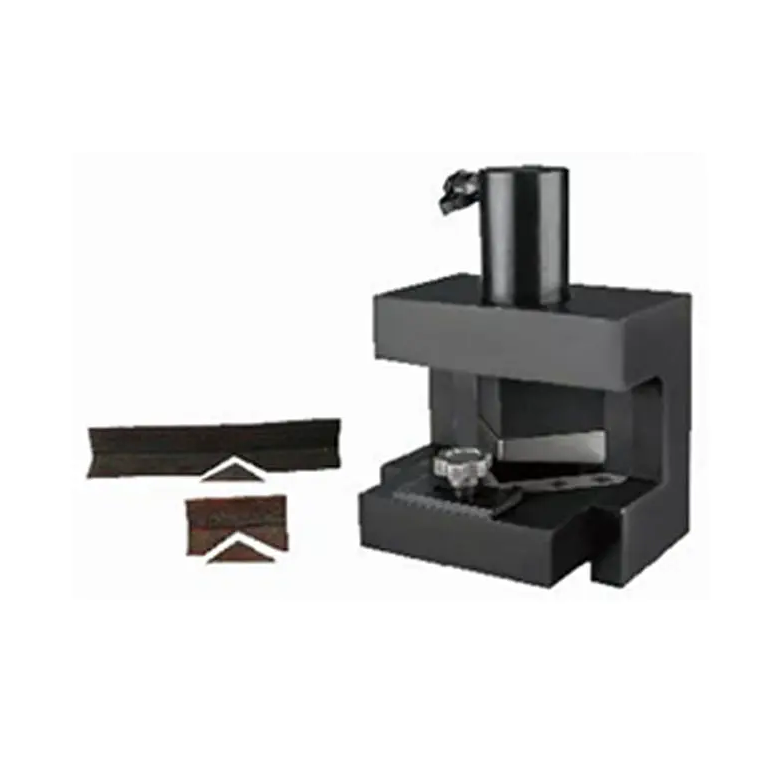
The cutting precision of a Hydraulic Angle Steel Cutter is a vital aspect that determines the quality and reliability of the final steel components. This type of machine is designed to produce clean, accurate cuts on angle steel, which is essential for applications in construction, manufacturing, and engineering. Ensuring cutting precision involves a combination of advanced mechanical design, hydraulic system control, blade quality, and regular maintenance, all of which contribute to the consistent performance of the Hydraulic Angle Steel Cutter.
Firstly, the fundamental factor in maintaining cutting accuracy lies in the hydraulic system itself. The Hydraulic Angle Steel Cutter utilizes hydraulic pressure to apply a powerful and consistent force to the cutting blade. Precise control of hydraulic pressure and flow rate ensures that the blade moves smoothly and steadily through the steel without sudden jerks or fluctuations. This controlled movement is critical to preventing irregular or imprecise cuts. Modern hydraulic systems often incorporate sensors and electronic controls to monitor and regulate pressure dynamically, thus maintaining optimal conditions for precise cutting.
The design and alignment of the cutting blade also play a crucial role in guaranteeing cutting precision. The blade must be manufactured to exact specifications, using high-quality materials capable of holding a sharp edge. Proper alignment of the blade relative to the angle steel ensures that the cut is straight and meets dimensional requirements. Manufacturers often include adjustable blade positioning features, allowing operators to fine-tune the blade’s angle and contact point to match specific cutting needs. This adaptability is important for maintaining precision across different sizes and types of angle steel.
Another significant aspect is the machine’s structural rigidity and stability. The frame and cutting assembly of the Hydraulic Angle Steel Cutter are engineered to minimize vibrations and deflections during operation. Excessive movement or vibration can cause deviations in the cutting path, resulting in inaccurate cuts. Heavy-duty materials and reinforced construction contribute to a stable cutting environment, helping to sustain precision even under continuous or heavy-duty use.
Operator skill and machine calibration are additional factors in achieving high cutting precision. Experienced operators know how to set up the machine correctly, adjust hydraulic pressure, and position the steel workpiece to ensure that cuts meet specifications. Routine calibration and maintenance, such as checking blade wear, tightening bolts, and verifying hydraulic pressure levels, are essential to keep the cutter operating at peak precision.
In addition, some advanced Hydraulic Angle Steel Cutters are equipped with computerized control systems or CNC integration, allowing for programmed cuts with very tight tolerances. These systems automate the cutting process and reduce human error, further enhancing precision and repeatability.
Lastly, proper maintenance directly influences cutting accuracy. Worn blades, hydraulic leaks, or contamination of hydraulic fluid can degrade performance and cause imprecise cuts. Regular inspection and timely replacement of worn parts ensure that the Hydraulic Angle Steel Cutter maintains its designed level of precision over time.
In conclusion, the cutting precision of a Hydraulic Angle Steel Cutter is ensured through a combination of precise hydraulic control, high-quality blade design and alignment, structural stability, skilled operation, advanced automation options, and diligent maintenance. These elements work together to provide reliable, accurate cutting performance, making the Hydraulic Angle Steel Cutter an essential tool for industries requiring exact angle steel fabrication.
The corner angle cutting machine is dedicated to angle cutting, bending, and cutting of the multi-functional hydraulic angle iron processing machine, as long as the replacement tooling mold is on the line. It is a new type of hydraulic tool, mainly used for power systems (engineering, maintenance, tower fill), bridges, and telecommunications. geology. construction and installation industries, such as field operations.
- Art
- Causes
- Crafts
- Dance
- Drinks
- Film
- Fitness
- Food
- Games
- Gardening
- Health
- Home
- Literature
- Music
- Networking
- Other
- Party
- Religion
- Shopping
- Sports
- Theater
- Wellness
