Exploring the Advanced Capabilities of a Pressure Control Factory’s Products Under Harsh Operating Conditions
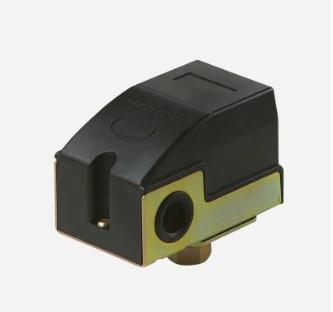
Operating in high-temperature and high-pressure environments is one of the most demanding challenges across industrial sectors such as oil and gas, power generation, chemical processing, and aerospace. These settings expose equipment to extreme stress that can rapidly degrade performance and compromise safety if not properly addressed. For this reason, selecting a Pressure Control Factory that can manufacture robust, reliable, and precise products for such conditions is essential. The performance of a pressure control system under these extremes reflects the engineering depth, materials expertise, and technological sophistication of the Pressure Control Factory behind it.
A reputable Pressure Control Factory understands that high-temperature environments—often exceeding 400°C (752°F)—demand specially engineered materials and design considerations. Components must resist thermal expansion, seal degradation, and mechanical fatigue. Pressure regulators, valves, and sensors designed for such environments typically incorporate high-grade alloys like Inconel, Hastelloy, or stainless steel with high-temperature ratings. These materials maintain structural integrity and resist oxidation even under prolonged exposure to heat. In many cases, internal seals and diaphragms are made from high-performance elastomers such as Viton or metal bellows designed to withstand thermal cycling without losing elasticity or developing leaks.
In high-pressure scenarios—ranging from hundreds to thousands of bar—a Pressure Control Factory must design systems that not only contain pressure safely but also control it with extreme precision. This requires meticulous engineering of critical components such as valve seats, springs, and actuators to ensure they operate within narrow tolerances despite immense force. Advanced manufacturing techniques like CNC machining and electron-beam welding are often employed to create components capable of withstanding high pressure without distortion or failure. Additionally, pressure transducers used in these environments must be built with robust housings and hermetically sealed sensor elements to maintain accuracy and reliability.
Thermal and pressure extremes often occur simultaneously, creating complex interactions that can lead to seal leakage, sensor drift, or valve malfunction. A top-tier Pressure Control Factory anticipates these issues through finite element analysis (FEA) and computational fluid dynamics (CFD) simulations during the design phase. These tools allow engineers to predict how materials and assemblies will behave under operational stress, enabling proactive reinforcement and design optimization. Furthermore, many factories perform extensive in-house testing using pressure chambers and thermal ovens to simulate real-world environments before releasing products to the market.
In addition to raw durability, control precision remains a critical metric. Even in extreme environments, industries demand exact pressure regulation to ensure process stability and product quality. Advanced Pressure Control Factory systems integrate smart digital controls with adaptive algorithms capable of maintaining steady output despite external fluctuations. These systems often feature temperature compensation and self-correcting functions that keep pressure variations within strict tolerances. The integration of IoT and remote monitoring technologies further enhances their functionality, allowing operators to track performance and receive alerts for preventative maintenance in real time.
Finally, compliance with international safety and performance standards is a non-negotiable aspect of operating in extreme conditions. Leading Pressure Control Factory operations adhere to certifications like ASME, PED, ATEX, and ISO 9001, which guarantee that their products have undergone rigorous testing and meet industry requirements for high-temperature and high-pressure performance. This not only assures buyers of the product’s reliability but also facilitates regulatory approvals in global markets.
The device's working principle involves dual control of Pressure and flow. The water pump turns on and off automatically when the water pressure changes based on water consumption.
- Art
- Causes
- Crafts
- Dance
- Drinks
- Film
- Fitness
- Food
- Oyunlar
- Gardening
- Health
- Home
- Literature
- Music
- Networking
- Other
- Party
- Religion
- Shopping
- Sports
- Theater
- Wellness
