Why Circumferential Aeration Aerator Offers a Significant Energy Advantage Over Conventional Aerators
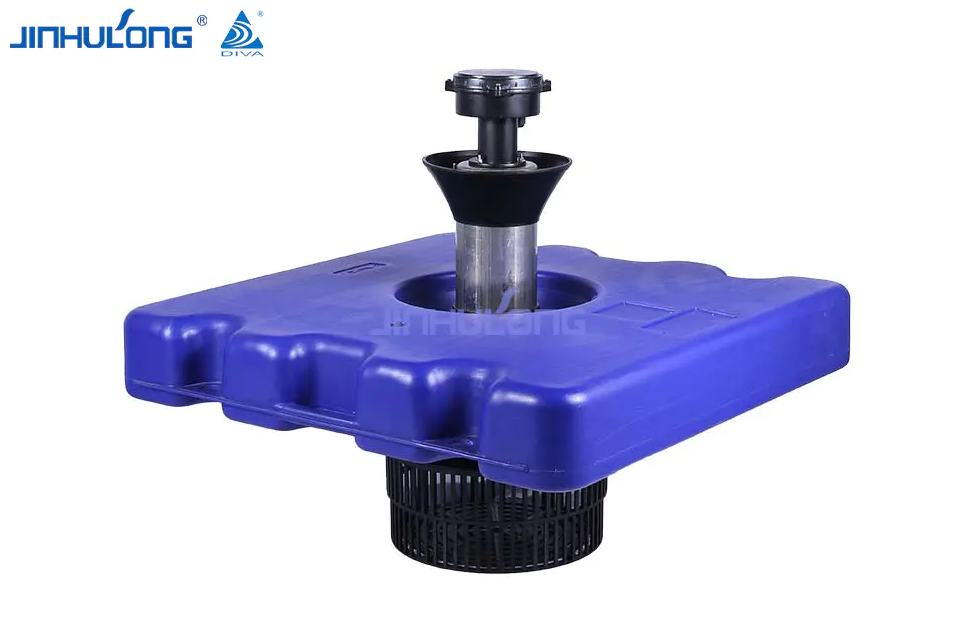
Energy efficiency has become a central focus in the field of water treatment, aquaculture, and environmental management. Among the various operational components in these sectors, aeration systems represent one of the most energy-intensive processes. Therefore, innovations that improve energy utilization without compromising performance are increasingly valued. One such innovation is the Circumferential Aeration Aerator, which has demonstrated clear advantages over traditional aeration machines in terms of power consumption. This article will explore how and why the Circumferential Aeration Aerator outperforms conventional systems in energy efficiency, offering both environmental and economic benefits.
The core reason behind the superior energy performance of the Circumferential Aeration Aerator lies in its optimized air dispersion mechanism. Unlike traditional aerators, which often rely on large blowers, mechanical paddles, or coarse bubble diffusers, the Circumferential Aeration Aerator utilizes a 360-degree radial diffusion system that maximizes oxygen transfer per unit of energy input. This design allows air to be released in fine, evenly distributed bubbles, greatly increasing the surface area of contact between air and water. Finer bubbles have a longer residence time in the water column, which improves oxygen absorption and reduces the amount of air required to maintain desired dissolved oxygen (DO) levels.
Traditional aerators typically suffer from inefficient oxygen transfer due to large, fast-rising bubbles or turbulent mechanical action that prioritizes agitation over actual aeration. These methods waste a considerable portion of the energy supplied to the system, as much of the oxygen escapes before being dissolved. Consequently, these systems often require higher horsepower motors or larger air compressors to compensate for their inefficiencies. In contrast, the Circumferential Aeration Aerator achieves higher oxygen transfer efficiency (OTE), sometimes reaching values above 6 kg O₂/kWh, depending on the application, while many traditional systems struggle to exceed 2–3 kg O₂/kWh under similar conditions.
Additionally, the intelligent hydraulic design of the Circumferential Aeration Aerator minimizes head loss and back pressure in the system. This means that the equipment can operate effectively at lower pressures, requiring less energy to move air through the system. Some models also incorporate variable-speed drives and real-time oxygen monitoring systems, which automatically adjust the aerator’s operation based on demand. This dynamic adjustment further improves energy efficiency, especially in systems with fluctuating biological oxygen demand (BOD) or seasonal changes in temperature and organic load.
Another major contributor to energy savings is the reduced need for additional mixing equipment. Many traditional systems require supplemental mixers to ensure uniform DO distribution, especially in large or irregular tanks. The radial flow pattern created by the Circumferential Aeration Aerator inherently promotes both vertical and horizontal mixing, making these extra devices unnecessary. Fewer devices mean lower cumulative power consumption and reduced operational complexity.
The lifecycle energy cost of aeration is also significantly lower with the Circumferential Aeration Aerator. Since the system is designed with fewer moving parts and is often less prone to clogging and fouling, it maintains optimal performance over time without requiring excessive maintenance or overcompensation with higher power settings. This leads to consistent energy savings and fewer unplanned downtimes, which indirectly contributes to improved overall plant efficiency.
- Art
- Causes
- Crafts
- Dance
- Drinks
- Film
- Fitness
- Food
- Spellen
- Gardening
- Health
- Home
- Literature
- Music
- Networking
- Other
- Party
- Religion
- Shopping
- Sports
- Theater
- Wellness
