The Benefits of Using Custom Grinding Wheels in Manufacturing
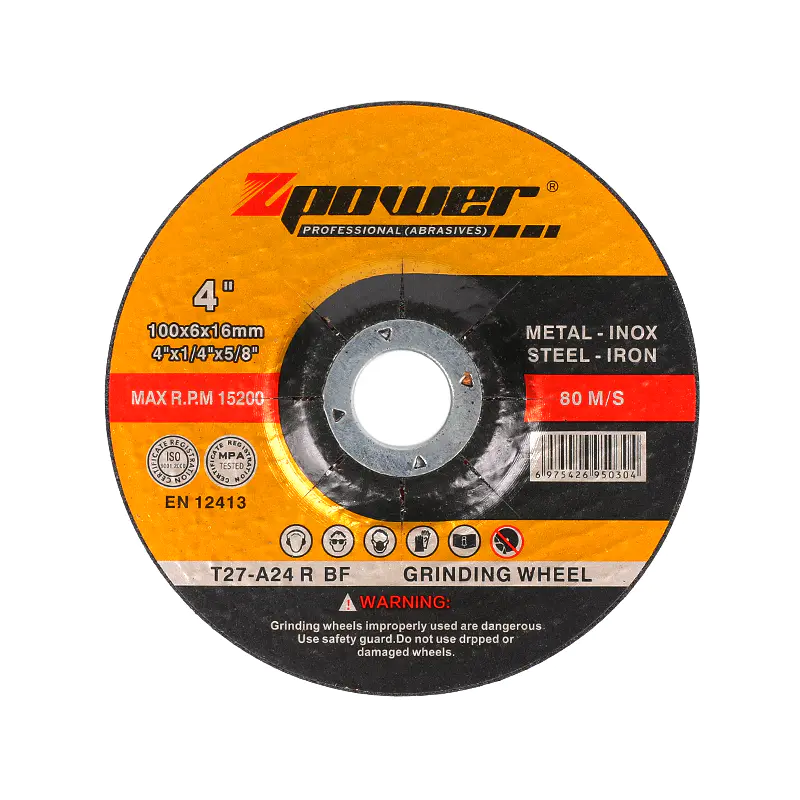
In various manufacturing and metalworking industries, the use of custom grinding wheels has become increasingly important for achieving specific results in grinding and finishing processes. Unlike standard grinding wheels, custom grinding wheels are designed and produced to meet particular requirements, offering tailored solutions for unique applications.
One of the primary advantages of custom grinding wheels is their ability to adapt to the exact needs of a job. Different materials, shapes, and sizes are available to address distinct surface finishes, tolerances, and grinding speeds. This flexibility allows manufacturers to improve efficiency and maintain consistent quality in their products.
Custom grinding wheels can be manufactured using a variety of abrasive materials, including aluminum oxide, silicon carbide, and diamond. Each abrasive type suits different applications and materials. For example, diamond custom grinding wheels are often preferred for grinding hard materials like ceramics and carbides, while aluminum oxide wheels work well on steel and other metals.
The design of a custom grinding wheel also plays a crucial role in its performance. Factors such as grit size, bonding material, and wheel hardness are tailored to the specific operation. These adjustments help control the grinding process, reduce wear, and extend the life of the wheel, which benefits both cost and production efficiency.
In industries such as aerospace and automotive manufacturing, where precision is critical, custom grinding wheels allow for the achievement of tighter tolerances and superior surface finishes. Customization helps reduce rework and scrap rates, contributing to more reliable manufacturing cycles and cost savings.
Another important consideration when selecting custom grinding wheels is their compatibility with grinding machines. Wheels designed for specific machines and operational speeds ensure safer and smoother operation. This compatibility reduces the risk of wheel damage or accidents, which can interrupt production and increase maintenance costs.
Maintenance and monitoring of custom grinding wheels are necessary to maintain performance and safety. Regular inspections help identify wear patterns, cracks, or imbalance issues that could affect grinding quality. Proper dressing and balancing of the wheel ensure consistent results and extend its useful life.
Customization also allows for innovation in grinding processes. For example, some applications require grinding wheels with specialized shapes or multiple layers of abrasive materials. These unique designs are only possible through custom manufacturing, enabling companies to address challenges that standard wheels cannot solve.
Cost-effectiveness is another aspect that businesses consider when choosing custom grinding wheels. While the initial investment may be higher compared to off-the-shelf wheels, the tailored design can improve operational efficiency, reduce downtime, and lower overall expenses related to wheel replacement and maintenance.
Custom grinding wheels offer significant advantages for industries seeking precision, durability, and efficiency in their grinding processes. By tailoring abrasive material, design, and specifications, these wheels provide solutions that standard options often cannot match. For manufacturers looking to enhance product quality and operational performance, custom grinding wheels represent a valuable component of their production toolkit.
https://www.cuttingdiscfactory.com/product/abrasive-wheels/resin-grinding-discs/
- Art
- Causes
- Crafts
- Dance
- Drinks
- Film
- Fitness
- Food
- Juegos
- Gardening
- Health
- Inicio
- Literature
- Music
- Networking
- Otro
- Party
- Religion
- Shopping
- Sports
- Theater
- Wellness
