A Manufacturer’s View on Ball Valve Production and Applications
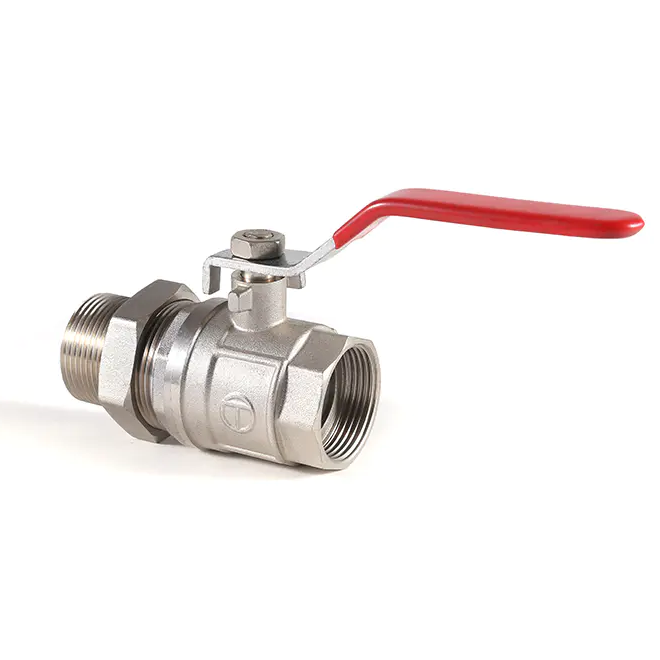
Ball valves are critical components used widely in various fluid control systems. From a manufacturing standpoint, producing ball valves involves careful consideration of design, material selection, precision machining, and quality assurance to ensure that the final product meets the demands of diverse applications.
One of the essential elements in manufacturing ball valves is the choice of materials. Depending on the intended application, materials must provide adequate strength, corrosion resistance, and durability. Common materials include stainless steel, brass, and various alloys, each selected based on environmental conditions such as pressure, temperature, and the type of fluid being controlled. Manufacturers work closely with suppliers to source materials that maintain consistency and meet required standards.
Design plays a significant role in the manufacturing process. Ball valves typically consist of a spherical ball with a hole in the center that controls flow when rotated. The precision in machining this ball and the valve body affects the sealing capability and ease of operation. Manufacturers invest in CNC machining and advanced finishing processes to achieve tight tolerances, ensuring that the valve operates smoothly and provides reliable sealing to prevent leaks.
Assembly is another important step. The internal components such as seats, seals, and stems must be assembled carefully to maintain performance and extend service life. Manufacturers often employ automated assembly lines combined with manual inspection to balance efficiency and quality. Attention to detail during assembly reduces the chances of malfunction and supports consistent valve operation.
Testing and quality control are integral parts of the manufacturing process. Ball valves undergo pressure tests, leak tests, and operational tests to verify their functionality under specified conditions. This ensures that each valve leaving the production line adheres to established performance criteria. Manufacturers implement standardized testing protocols to provide customers with reliable products suited for their specific needs.
Customization is also a consideration for manufacturers. Different industries and applications may require specific valve sizes, pressure ratings, or connection types. Manufacturers offer customization options to meet these varied requirements, adapting production techniques accordingly. This flexibility enables ball valves to be used in sectors such as oil and gas, water treatment, chemical processing, and HVAC systems.
Sustainability and cost efficiency are further factors influencing manufacturing practices. Efficient use of raw materials, waste reduction, and energy-saving production methods contribute to a more responsible manufacturing approach. Additionally, manufacturers focus on streamlining production processes to provide valves that balance quality with cost-effectiveness.
In conclusion, manufacturing ball valves demands a combination of material expertise, precise engineering, thorough assembly, and rigorous testing. These elements together help ensure that the valves meet the operational expectations of users across many industries. By maintaining focus on quality and adaptability, manufacturers support the continued relevance and application of ball valves in fluid control systems worldwide.
- Art
- Causes
- Crafts
- Dance
- Drinks
- Film
- Fitness
- Food
- Games
- Gardening
- Health
- Home
- Literature
- Music
- Networking
- Other
- Party
- Religion
- Shopping
- Sports
- Theater
- Wellness
