The Role of Alloy Selection in Aluminium Circles for Spinning
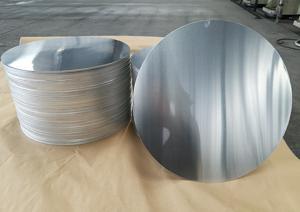
When it comes to aluminium spinning, the choice of alloy plays a crucial role in determining the success of the forming process. Not all aluminium alloys are suitable for spinning, as each has distinct mechanical properties that affect formability, strength, and surface finish. Understanding the best alloys for spinning can help manufacturers achieve high-quality spun products with minimal defects.
Why Alloy Selection Matters in Spinning
Aluminium spinning involves shaping a flat aluminium circle into a symmetrical part using a lathe and specialized tools. The material must exhibit excellent ductility to withstand deformation without cracking. Additionally, it should have sufficient strength to maintain structural integrity after forming.
The most commonly used alloys for spinning include:
1. 1050 & 1060 (Pure Aluminium)
Excellent formability due to high ductility.
Low strength, making them ideal for simple shapes like cookware and light reflectors.
Soft and easy to work with but may require annealing during deep spinning.
2. 3003 (Manganese-Alloyed)
Better strength than pure aluminium while retaining good formability.
Resistant to corrosion, making it suitable for chemical and food processing equipment.
Requires intermediate annealing in multi-stage spinning operations.
3. 5052 & 5083 (Magnesium-Alloyed)
Higher strength and good corrosion resistance.
Suitable for marine and automotive applications where durability is key.
More challenging to spin than 1xxx or 3xxx alloys, often requiring controlled heating.
Factors Influencing Alloy Choice
Part Complexity: Simple shapes can use softer alloys, while complex geometries may need stronger materials with intermediate annealing.
End-Use Requirements: If the spun part needs to withstand pressure or harsh environments, 5xxx or 6xxx alloys may be preferred.
Cost Considerations: Pure aluminium is cheaper but may not meet mechanical demands, while high-strength alloys increase production costs.
Conclusion
Selecting the right aluminium alloy for spinning ensures smoother production, fewer defects, and better performance of the final product. Manufacturers must balance formability, strength, and cost to achieve optimal results.
- Art
- Causes
- Crafts
- Dance
- Drinks
- Film
- Fitness
- Food
- Juegos
- Gardening
- Health
- Inicio
- Literature
- Music
- Networking
- Otro
- Party
- Religion
- Shopping
- Sports
- Theater
- Wellness
