When Turning Steel Parts With a CNC Machine, What Secondary Operations Are Possible?
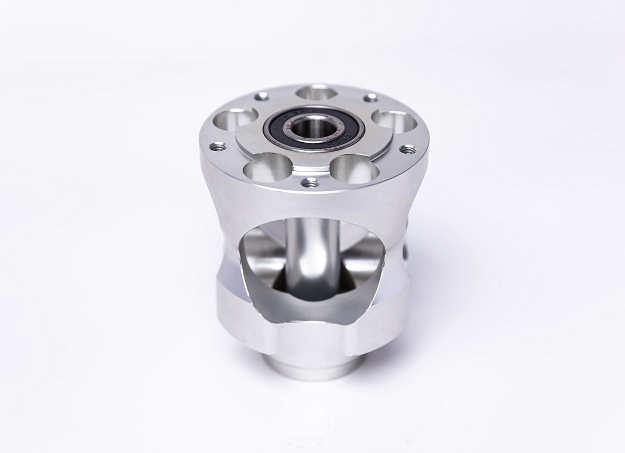
Secondary operations are any operations performed on CNC turning steel parts after the initial machining procedure. Enhancing the part's performance, tolerances, appearance, or finish is the goal of these operations. Some of the most common secondary operations for CNC turning steel parts include:
l Heat treatment: Heat treatment can alter the mechanical properties of steel, such as its toughness, strength, and hardness. Common heat treatments for steel parts that are CNC turning include annealing, normalizing, hardening, and tempering.
l Surface finishing: Surface finishing procedures are used to improve the part's surface functionality and/or appearance. When CNC turning steel parts, surface finishing techniques like polishing, buffing, grinding, and plating are commonly employed.
l Deburring: Taking burrs and sharp edges out of a machined item is the process of deburring. Brushing, tumbling, and vibratory finishing are typical deburring methods for steel parts that are CNC turning.
l Hardware installation: Hardware installation is the process of attaching fasteners, such as bolts, nuts, screws, and inserts, to a machined component. Typically, broaching, threading, and tapping are used to install hardware on CNC turning steel parts.
When designing a CNC turning steel part, it is imperative to consider the secondary operations required to achieve the proper performance, tolerances, and finish. By being aware of the secondary operations that are available, designers can create parts that are easier to manufacture and cost less. If a CNC turning steel part has a problem—such as a dimensional error or a poor surface finish—it is helpful to know what secondary operations were performed on it. This information can be used to identify the root cause of the issue and develop a solution.
- Art
- Causes
- Crafts
- Dance
- Drinks
- Film
- Fitness
- Food
- Jocuri
- Gardening
- Health
- Home
- Literature
- Music
- Networking
- Alte
- Party
- Religion
- Shopping
- Sports
- Theater
- Wellness
