Unleashing the Full Potential of Carbide Rotary Burs in Timber Processing
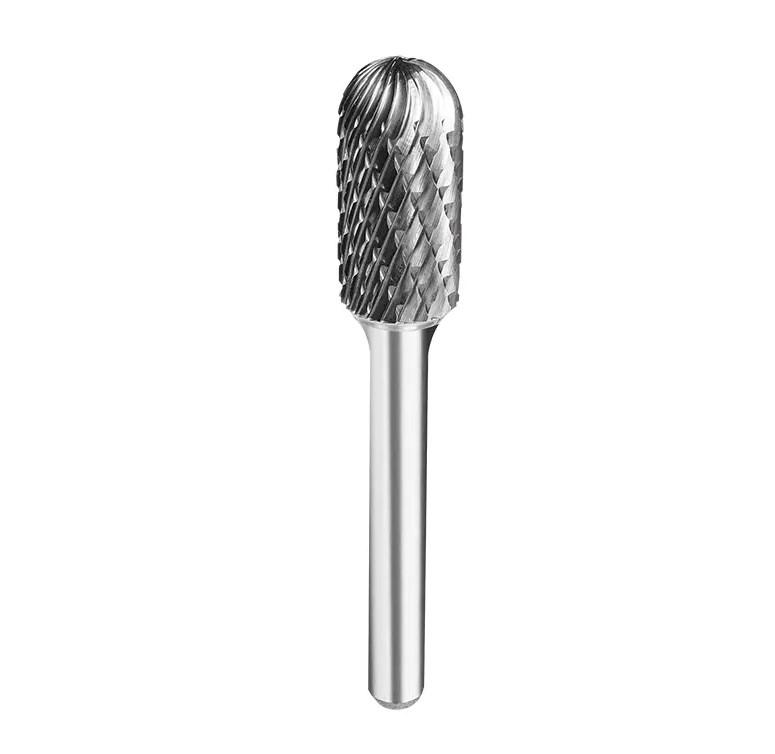
Carbide Rotary Burs are highly versatile tools that have become an integral part of woodworking due to their ability to cut, grind, and shape wood with precision and efficiency. Ensuring their optimal performance in this context is crucial for achieving high-quality results and maintaining the longevity of the tools. This article delves into the various factors that contribute to the performance of Carbide Rotary Burs in woodworking and offers practical advice on how to maximize their effectiveness.
The starting point for ensuring the performance of Carbide Rotary Burs in woodworking is selecting the appropriate bur type for the specific task. Different wood types, such as hardwoods and softwoods, require burs with varying levels of hardness and durability. For instance, a bur with a coarser grit is suitable for roughing out large areas in softwoods, while a finer grit bur is ideal for detailed work and finishing in hardwoods.
Proper maintenance of Carbide Rotary Burs is another critical aspect that affects their performance. Regular inspection of the burs for any signs of wear and tear is essential. Dull burs not only reduce the quality of work but also increase the risk of accidents due to the tool losing its grip on the wood or causing uneven cuts. When a bur shows signs of excessive wear, it is time to replace it with a new one or sharpen it if possible.
The speed at which Carbide Rotary Burs are operated can significantly impact their performance. High-speed rotation can lead to overheating, which may cause the wood to burn or the bur to break. On the other hand, too slow a speed can result in excessive friction, leading to a poor finish and potential damage to the bur. Therefore, it is crucial to use the recommended speed for the specific type of wood and the bur being used.
The cutting angle of Carbide Rotary Burs is another factor that should not be overlooked. The angle at which the bur is held against the wood surface can affect the quality of the cut and the ease of the operation. A steeper angle may be necessary for aggressive cutting, while a shallower angle is preferred for more delicate work. Adjusting the angle according to the task can help achieve cleaner cuts and reduce the risk of the bur binding in the wood.
The use of appropriate cutting oils or lubricants can also enhance the performance of Carbide Rotary Burs in woodworking. These fluids help to reduce friction, prevent the wood from burning, and extend the life of the burs. It is important to select the right lubricant for the type of wood being worked on and to apply it correctly to ensure optimal results.
Lastly, operator skill and experience play a significant role in the performance of Carbide Rotary Burs. A skilled woodworker will know how to handle the burs with precision, apply the right amount of pressure, and make smooth, controlled movements to achieve the desired outcome. Training and practice are essential for ensuring that Carbide Rotary Burs perform at their best in woodworking applications.
In conclusion, the performance of Carbide Rotary Burs in woodworking is influenced by a combination of factors, including the selection of the right bur, maintenance practices, operational speed, cutting angle, use of lubricants, and the skill of the operator. By paying attention to these aspects and following best practices, woodworkers can ensure that their Carbide Rotary Burs deliver the best possible results, every time.
https://www.carbidebursfactory.com/product/carbide-rotary-burs-metric/
- Art
- Causes
- Crafts
- Dance
- Drinks
- Film
- Fitness
- Food
- الألعاب
- Gardening
- Health
- الرئيسية
- Literature
- Music
- Networking
- أخرى
- Party
- Religion
- Shopping
- Sports
- Theater
- Wellness