What measures can be taken to lessen the severity of these effects
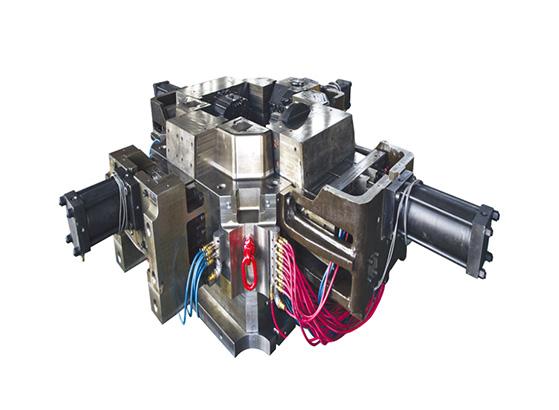
Metal Plating 1. The temperature of the heating process that is used for the quenching can be lowered by forty degrees Celsius if necessary in order to achieve the desired results.
When high-carbon steel is put through processes that involve rapid heating at a low temperature for a short amount of time, followed by quenching, the amount of carbon that is contained in austenite can be reduced. Because of this, it is possible to produce lath martensite, which is superior to other types of martensite in terms of its tenacity as well as its strength. Carbonitriding is used on some transmission gears instead of carburizing because carbonitriding has the additional benefit of reducing the amount of deformation that is caused by heat treatment. Carburizing is still used on other transmission gears. This has the additional advantage of reducing the overall amount of deformation that is brought about as a result of the effect.
2. 0~1. If the value of could be brought down, the amount of time needed to heat the substance could be reduced by a sizeable amount, which would be beneficial. When time is of the essence, it would be helpful to have something like this available to you, and it would be helpful to have something like this at your disposal. Experiments need to be carried out in order to determine how long the heating time ought to be for the steel-type zinc alloy die-casting part in order to determine how long the heating time ought to be for the steel-type zinc alloy die-casting part. In these experiments, it is necessary to take into consideration a variety of factors, including the size of the component being analyzed, the amount of charging that is introduced into the furnace, and any other pertinent considerations.
3. Either refrain from heating the product at all, or reduce the frequency with which you subject it to heating.
Put an immediate stop to the process of tempering the carburized steel as soon as possible.When working with high-speed steel, it is possible to reduce the number of temperings that are carried out; for instance, W18Cr4V steel machine saw blades only require a single tempering as opposed to the standard 560°C tempering that is performed on them.The product's lifespan can be extended by a factor of forty percent if it is subjected to three cycles of heating and cooling within the same time frame (one hour).The hardness has been maintained at approximately 45HRC throughout, significant improvements have been made to the product's strength and wear resistance, and the product's quality has been maintained throughout the entire process.Utilizing the set becomes a lot less complicated when the 20 steel is in the quenched state.
4.
5. The results of the measurement of the stress were used to determine the required depth of the hardened layer, and the results showed that the hardened layer that was already present was too deep. In addition, the findings demonstrated that the traditional hardened layer needed to be only 70 percent as deep as originally thought in order to be adequate for the job. It is also possible to save twenty percent of the energy that is used if the depth of the permeable layer can be controlled to the lower limit of the technical requirements in actual production. This would bring the total amount of energy savings to forty percent. Because of this, the overall amount of energy that could be saved would increase to forty percent. In addition to cutting down on the amount of time necessary for production and the amount of deformation that takes place during production, this will make it possible to save energy.
6. To treat the material, apply a chemical heat treatment. This type of treatment involves using high temperatures in conjunction with a vacuum.
The purpose of the high-temperature chemical heat treatment is to raise the temperature of the chemical heat treatment under specific conditions, specifically when the operating temperature of the equipment permits it and the austenite grains of the steel that is to be infiltrated do not grow. This is done in order to achieve the desired result of the high-temperature chemical heat treatment.In order to accomplish the goals that are set for the chemical heat treatment carried out at high temperatures, this step is taken.The next step is carried out in order to achieve the objectives that have been established for the chemical heat treatment that is carried out at high temperatures.Because of this fact, zinc die casting products the rate at which the steel is carburized is sped up by a sizeable amount, which is a direct consequence of the fact itself.Even though there are still a great many problems, there is still the possibility of even further development. This is despite the fact that there are still a great many issues.However, this is made significantly more difficult by the fact that there are still a great many issues to be resolved.The chemical heat treatment that is performed in a vacuum does so in a gas phase medium that is subjected to a pressure that is comparable to that of a vacuum. This creates the conditions necessary for the treatment to be successful.
7. A chemical reaction that takes place at high temperatures, involves the use of ions and other substances, and the reaction itself involves multiple components.
It is a chemical heat treatment process that uses glow discharge between the workpiece and the anode to simultaneously infiltrate the elements to be infiltrated in the gas phase medium containing the elements to be infiltrated at a pressure lower than one atmosphere. This is done at a pressure that is lower than one atmosphere.This takes place at a pressure that is lower than one atmosphere throughout the entire process.This process is able to take place because the pressure in this location is lower than one atmosphere.This strategy offers a number of benefits, such as a high rate of penetration, the production of results of a high quality, and a reduction in the amount of energy that is required to carry it out. These are just some of the benefits.You might want to think about incorporating a process known as induction self-tempering into your workflow.
In the past, tempering in the furnace was the standard method, but in recent years, induction self-tempering has taken its place as the standard method due to its superior efficiency.It is possible to temper an object in a relatively short amount of time due to the fact that the remaining heat is not completely removed during the quenching and cooling process.Because of this, the process can be carried out without any problems.
9. It is possible to eliminate the drawbacks of using post-forging waste heat quenching as the final heat treatment, such as coarse grains and poor impact toughness, by using high-temperature tempering as a pretreatment in addition to using post-forging waste heat quenching as the final heat treatment. This is because coarse grains and poor impact toughness are caused by using post-forging waste heat quenching as the final heat treatment.This is due to the fact that the final heat treatment being used, post-forging waste heat quenching, causes the grains to be coarse and results in a material with poor impact toughness.Instead of carburizing and quenching the whole thing, it is recommended that you just quench the surface of the material.
An in-depth analysis of the myriad of ways in which low, medium, and high carbon steels, with carbon contents ranging from 0.6% to 0.8%, manifest the properties that are associated with their namesake metals.In order for us to be successful in the production of gearbox gears, we made the decision to switch from the traditional carburizing and quenching process, which used 20i steel, to a high-frequency quenching method, which used 40Cr steel. This allowed us to successfully manufacture gearbox gears.Because of this, we were able to achieve much better results.Because of this, we were able to accomplish much more than we initially anticipated with regard to the results of our effort.We need to have a general idea while we are in the process of formulating the process, and we need to be closely integrated with the economic benefits that the company has to offer while we are in this process.
- Art
- Causes
- Crafts
- Dance
- Drinks
- Film
- Fitness
- Food
- Games
- Gardening
- Health
- Home
- Literature
- Music
- Networking
- Other
- Party
- Religion
- Shopping
- Sports
- Theater
- Wellness
