An Article To Quickly Learn Captive Fastener And Screw
Screws are essential for keeping objects together so machines or devices can function properly. The various types of fastener you choose will depend on what type of project you’re working on. There are many types of captive fasteners that are useful for tightening different objects and they play a crucial role in the production of products and goods. A captive fastener is a special screw that locks into a pre-drilled hole in order to create a permanently secure hold. They feature a head and external threading similarly seen on small screws. They’re different because they can be fastened and unfastened without having to remove it from the pilot hole. There are several methods in which these micro screws are manufactured. These include press-fitting, broaching, and thread locking.
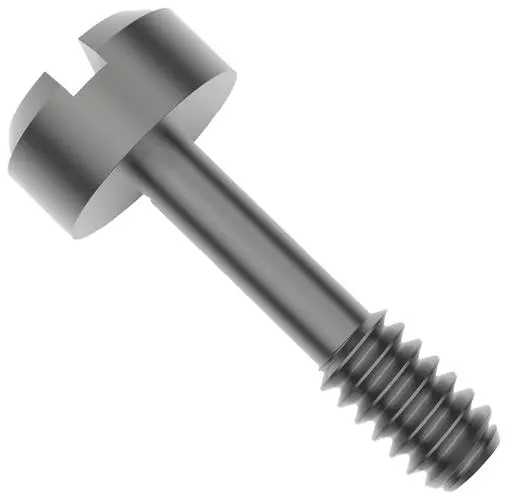
Benefits
There are a few benefits with using custom fasteners. Because of the permanent hold, they create with the pilot hole, these screws are less likely to suffer from age-related degradation. They also offer a high level of protection against stress and vibration that can loosen traditional screws. Captive fasteners are ideal for manufacturing companies due to their inexpensive cost.
Features
Captive fasteners include either self-clinching or broaching features. Self-clinching features are typically used for ductile materials for use in printed circuit board fastening and sheet metal integration. Broaching features are used for non-ductile materials. The captive fastener accomplishes joining through an interference fit at the time of installation. Each type becomes a permanent part of the item or panel which it’s installed.
A captive fastener can be valuable because of their speed in use in the manufacturing process. They can also keep costs low during field servicing. The type of custom fastener you use will depend on the sheet material or panels being used. When choosing custom fasteners, make sure they’re compatible and their hardness is greater than the material.
Types
1. Captive nuts
Captive nuts are fasteners that are internally-threaded. It’s a nut that is wrapped up in a spring steel cage. They’re designed to quickly connect with studs. These fasteners are effective for blind locations and are usually able to be attached without doing damage to panel finishes. In contrast with threaded holes, captive nuts can be replaced if they’re over tightened, and are easier to use on materials that are too soft to be threaded. This specific fastener is typically utilized in industrial and electronic applications. They mount equipment in square-holed racks.
2. Weld nuts
A weld nut is a fastener that is designed for welding to another object. It’s usually made of stainless steel or low carbon steel. There are several kinds of these fasteners that can be used for various applications. Single tab weld nuts are used for heavier gage materials. Retainer weld nuts have a floating nut that is held within a retainer. This design allows for misaligned or off-center screws to be installed. The nut floating freely helps to compensate for any building inconsistencies. Other types of weld nuts that are used include four projection weld nuts, twin pilot weld nuts, and slab base nuts.
3. Captive screws
Captive screws are fasteners that are used in equipment panel assemblies and PC boards. These include signs, network cabinets, medical devices, and electronic enclosures. You can usually identify them by their threaded end and unthreaded shank. The design allows it to be locked into pre-drilled holes in order for the screw to be unfastened and fastened without any detachment. Captive screws can be combined with springs, retainers, and washers to put together a self-captivating assembly. These captive fasteners can be effective in fastening applications where vibration shock, thermal expansion, and thermal conductivity are involved. In addition, captive screws are useful in situations where quick assembly and disassembly is required, and they can prevent screws from falling into electrical circuits or getting lost.
Custom captive fastener
Whether you are working on a small house chore or a major industrial project, the screws used in executing the work will matter. Your project may require a custom captive screw, or it may require custom screws. Your options range from micro screws to tiny screws and more. Fortunately, the nut, bolt & screw industry has a wide range of options for you to choose from. Here is a look at some screws and their functions.
Screw Point Types
There are many different kinds of screw points. Each one is designed for a particular type of use, ranging from sheet metal to wood. Here are the five most common types groups of screw points. Machine and tapping screws, self-drilling screws, thread forming screws, thread cutting screws, and tapping screws. It is important to note that within each category there are several different types of points, each designed for a specific function.
Plastic Thread Forming Screws
Thread forming screws for plastic are in great demand today. For instance, the captive screw is a fastener that has been created to fit into holes that have already been drilled. This is a low-stress method that lessens the impact and reduces the likelihood of losing screws or cracking off pieces of plastic. These thread forming screws (such as the captive thread fastener) are especially effective for use in cell phones, laptops, and other devices. They are durable for assembly and disassembly and they resist loosening caused by vibrations. Among the variety of plastic thread forming screws includes delta PT, Hi-lo, plastite, trilobular, and more. As with all screws, it is important to emphasize the Critical nature of torque screws to the proper value. If they are too tight, they risk breaking. And if they are not tight enough, the may become loose or disengage.
- Art
- Causes
- Crafts
- Dance
- Drinks
- Film
- Fitness
- Food
- الألعاب
- Gardening
- Health
- الرئيسية
- Literature
- Music
- Networking
- أخرى
- Party
- Religion
- Shopping
- Sports
- Theater
- Wellness