Efficiency in Steel Tube Cutting: Streamlining Production with Modern Machinery
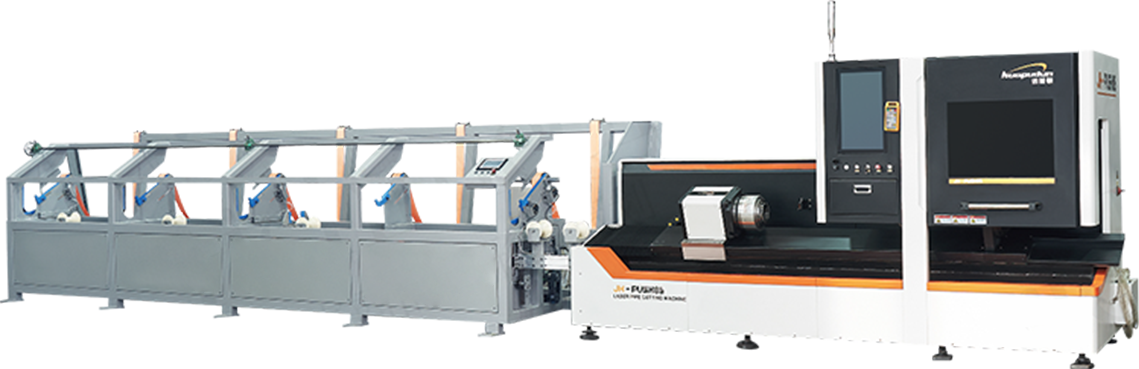
Efficiency is the lifeblood of any manufacturing operation. In the realm of steel tube cutting, efficiency translates to faster production times, reduced labor costs, and increased output. This article delves into how modern steel tube cutting machines are designed to optimize efficiency in the production process.
Laser cutting machines have become the industry standard for their ability to make clean, accurate cuts with minimal material loss. The use of a laser allows for intricate designs and complex patterns to be cut with ease, making it ideal for custom projects and prototypes.
The integration of automation and robotics into steel tube cutting machines has significantly increased efficiency. These machines can operate continuously, reducing downtime and labor costs. They also eliminate the need for manual handling, which can be both time-consuming and hazardous.
High-speed cutting technologies, such as high-frequency plasma cutting, have been developed to increase the speed of the cutting process. These machines can cut through steel tubes at a much faster rate than traditional methods, allowing for quicker production times.
Efficient material handling is a critical aspect of a streamlined production process. Modern steel tube cutting machines often come equipped with automated material handling systems that can load and unload tubes with minimal human intervention, further enhancing efficiency.
The steel tube cutting machine is a key player in the manufacturing industry, and its efficiency is crucial for the success of any production line. With the ongoing advancements in technology, these machines are becoming more efficient, allowing manufacturers to produce more with less, ultimately driving down costs and increasing competitiveness.
- Art
- Causes
- Crafts
- Dance
- Drinks
- Film
- Fitness
- Food
- الألعاب
- Gardening
- Health
- الرئيسية
- Literature
- Music
- Networking
- أخرى
- Party
- Religion
- Shopping
- Sports
- Theater
- Wellness