What Are Some Limitations of Wire EDM?
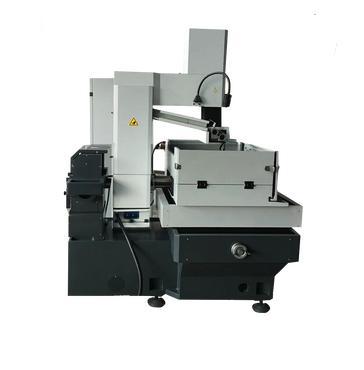
Wire EDM (Electrical Discharge Machining) is a powerful tool for creating precise and intricate parts, but it does have some limitations to consider when choosing a machining method. Here's a breakdown of some key drawbacks to keep in mind:
l Slower Cutting Speed: Compared to some other machining processes, Wire EDM can be slower, especially for thicker workpieces or intricate cuts with tight corners. The thin wire can only erode material at a limited rate, and complex geometries might require multiple wire paths, extending the machining time.
l Surface Finish: While generally good, the surface finish achieved with Wire EDM might require additional polishing or finishing steps depending on the application requirements. The spark erosion process can create a slightly textured surface, and achieving a mirror finish might not always be possible.
l Cost: Wire EDM machines can be expensive due to their complex technology and precise control systems. The cost of the wire itself, which needs to be replaced periodically, also contributes to the overall process cost. For simple parts, Wire EDM might not be the most cost-effective option compared to faster methods.
l Material Limitations: While it can handle a wide range of conductive metals, Wire EDM is not suitable for non-conductive materials like plastics, wood, or glass. The electrical discharge process relies on conductivity to remove material.
l Wire Breakage: Thin wires used in Wire EDM are susceptible to breakage, especially during rapid cutting or when encountering hard spots in the material. Breakage can lead to production delays and require re-threading the wire, adding downtime.
l Complexity for Simple Parts: For simple shapes or features, Wire EDM might be an overly complex and time-consuming process compared to methods like stamping, punching, or laser cutting. These alternative methods can be faster and more cost-effective for basic geometries.
In conclusion, Wire EDM excels at creating intricate parts from challenging materials with high precision. However, its limitations in terms of speed, surface finish, and cost need to be considered when choosing the most suitable machining method for your specific application. If production speed, cost-effectiveness, or a smooth surface finish are top priorities, alternative methods might be preferable for simpler shapes. Now I guess you might also want to get the differences between wire EDM and die-sinking EDM.
- Art
- Causes
- Crafts
- Dance
- Drinks
- Film
- Fitness
- Food
- Игры
- Gardening
- Health
- Главная
- Literature
- Music
- Networking
- Другое
- Party
- Religion
- Shopping
- Sports
- Theater
- Wellness
