What Are the Benefits of Using CNC Machined Aluminum?
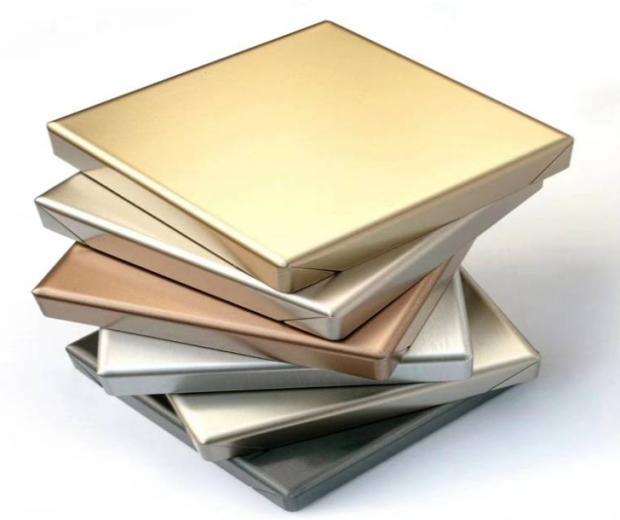
CNC-machined aluminum offers a compelling combination of properties that make it a popular choice for a wide range of applications across various industries. Here's a detailed breakdown of the key benefits that contribute to its widespread use:
Excellent Machinability
l Fast and Efficient Production: Aluminum is a soft and ductile metal, making it relatively easy to machine with CNC equipment. This translates to faster production times compared to machining harder metals. Manufacturers can create complex shapes and features with high precision using CNC machining techniques like milling, turning, and drilling.
l Reduced Manufacturing Costs: Faster machining times lead to lower production costs per unit. The ease of machining aluminum allows manufacturers to keep their processes efficient, contributing to overall cost-effectiveness.
l Design Flexibility: CNC machining allows for the creation of intricate and complex geometries in aluminum parts. This design freedom enables engineers to develop innovative and functional components that might not be possible with other manufacturing methods.
Superior Strength-to-Weight Ratio
l Lightweight Construction: Aluminum has a high strength-to-weight ratio, meaning it offers good structural strength while being significantly lighter than many other metals like steel. This lightweight property makes it ideal for applications where weight reduction is crucial.
l Improved Fuel Efficiency: In the automotive and aerospace industries, using lightweight aluminum components like engine blocks, wheels, and aircraft parts can significantly improve fuel efficiency. This translates to reduced fuel consumption, operational costs, and environmental impact.
l Enhanced Performance: The lighter weight of CNC-machined aluminum components can contribute to better overall product performance in various applications. For instance, lighter components in machinery can lead to faster acceleration and improved maneuverability.
Natural Corrosion Resistance
l Durable Material: Aluminum naturally forms a thin oxide layer on its surface, providing inherent protection against corrosion. This makes CNC-machined aluminum parts suitable for use in environments with exposure to moisture, air, or some mild chemicals.
l Reduced Maintenance Needs: The corrosion resistance of aluminum minimizes the need for additional coatings or special maintenance procedures to prevent rust or degradation. This translates to lower life-cycle costs for products made with CNC-machined aluminum.
l Applications in Diverse Environments: From marine components that can withstand saltwater to building facades exposed to weather, the corrosion resistance of aluminum allows its use in various environmental conditions.
Additional Advantages
l Good Electrical Conductivity: Aluminum is a good conductor of electricity, making it a valuable material for electrical components like heat sinks in electronic devices. These heat sinks efficiently dissipate heat away from sensitive electronic components, ensuring proper functioning.
l Recyclable Material: Aluminum is one of the most recyclable metals, with a high recycling rate. This eco-friendly characteristic makes CNC-machined aluminum a sustainable choice for manufacturers who prioritize environmental responsibility.
l Versatility: The combination of machinability, strength, and corrosion resistance makes CNC-machined aluminum a highly versatile material. It can be used in countless applications across various sectors, from consumer electronics to medical devices and industrial machinery.
In conclusion, the combination of excellent machinability, good strength-to-weight ratio, natural corrosion resistance, and other valuable properties make CNC-machined aluminum a preferred material for a vast array of applications. It offers manufacturers the ability to produce complex, lightweight, and durable parts in a cost-effective and sustainable manner. The article Building Stronger, Lighter Products With CNC Machined Aluminum will give you more information you might want to get.
- Art
- Causes
- Crafts
- Dance
- Drinks
- Film
- Fitness
- Food
- Games
- Gardening
- Health
- Home
- Literature
- Music
- Networking
- Other
- Party
- Religion
- Shopping
- Sports
- Theater
- Wellness
