What Is Anodizing?
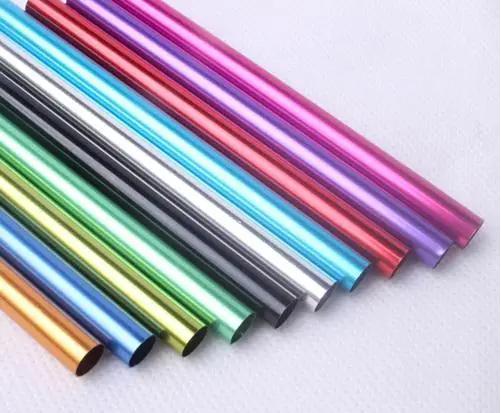
Anodizing is an electroplating technique that significantly enhances aluminum's properties by transforming its surface into a tougher, more corrosion-resistant layer. In simpler terms, it's a controlled method to thicken the natural oxide layer that already forms on aluminum when exposed to air. This aluminum oxide layer is incredibly strong and much more resilient to wear and tear than the base metal itself.
The process works by employing an electrochemical reaction. The aluminum piece is submerged in a special acidic bath (typically sulfuric acid) and transformed into the anode (positive electrode) within an electrical circuit. By running an electric current through the setup, oxygen ions are pulled from the electrolyte solution and bonded with the aluminum atoms on the surface. This reaction essentially cultivates a thicker and denser aluminum oxide layer.
Anodizing offers a multitude of advantages over bare aluminum. First and foremost, it dramatically improves the metal's resistance to corrosion. This makes anodized aluminum ideal for applications where exposure to harsh elements or chemicals is a concern, such as building materials for outdoor use, marine equipment, and components for electronic devices.
Anodizing also boasts significant aesthetic benefits. The anodized oxide layer can be left in its natural, slightly translucent state, or it can be dyed to create a vast array of vibrant and attractive colors. This versatility allows for the creation of visually appealing products while maintaining the superior performance characteristics.
Furthermore, anodizing enhances the wear resistance of aluminum. The resulting oxide layer is considerably harder than the base metal, making it more resistant to scratches, scuffs, and other forms of wear and tear. This improved durability is particularly valuable for applications that involve frequent handling or exposure to abrasive environments.
An additional benefit of anodizing is the improved electrical insulation properties it grants to aluminum. The aluminum oxide layer acts as a good electrical insulator, making anodized aluminum a suitable choice for applications where electrical conductivity needs to be controlled or minimized.
Overall, anodizing is a versatile and valuable process that significantly improves the functionality and aesthetics of aluminum. It offers superior corrosion resistance, enhanced wear resistance, a wider range of color options, and improved electrical insulation, making it a preferred choice for a vast array of applications in construction, manufacturing, and consumer goods. After you get what is the anodizing, you might get the part of the answer about What Are the Differences Between Anodizing and Painting?
- Art
- Causes
- Crafts
- Dance
- Drinks
- Film
- Fitness
- Food
- Games
- Gardening
- Health
- Home
- Literature
- Music
- Networking
- Other
- Party
- Religion
- Shopping
- Sports
- Theater
- Wellness
