How Does Viscosity Impact Orifice Plate Flow Meter?
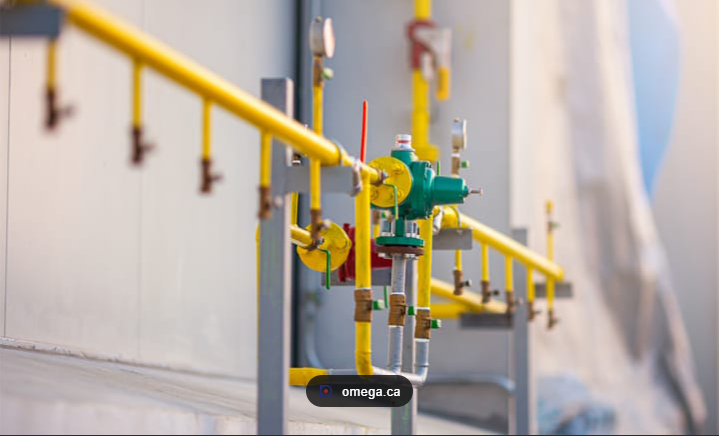
An orifice plate flow meter is one of the most widely used devices in flow measurement. Known for its simplicity, durability, and affordability, it measures flow by introducing a restriction in the pipeline, which causes a pressure drop. This pressure drop is then correlated to the flow rate using fluid dynamics principles.
However, despite its mechanical reliability, the orifice plate flow meter is not immune to variations in fluid properties. Among those properties, viscosity plays a significant role. The behavior of fluid through an orifice changes depending on how thick or thin it is. This article examines in detail how viscosity affects the operation and accuracy of an orifice plate flow meter, why this matters, and how to manage its influence.
Understanding Viscosity in Fluids
Viscosity is the measure of a fluid’s resistance to flow. A high-viscosity fluid, like honey, flows slowly. A low-viscosity fluid, like water, flows easily. There are two main types of viscosity: dynamic viscosity and kinematic viscosity. Dynamic viscosity measures the internal friction within a fluid. Kinematic viscosity accounts for both viscosity and density.
In practical terms, viscosity affects the way fluid particles interact with each other and with the surface of a pipe or flow meter. The thicker the fluid, the more resistance it presents to movement and the more it clings to surfaces.
In flow measurement, this becomes important because most devices, including the orifice plate flow meter, are based on assumptions about ideal fluid behavior. Real fluids, especially those with varying viscosity, can deviate from those assumptions.
Basic Operation of an Orifice Plate Flow Meter
An orifice plate flow meter works by placing a thin plate with a hole (the orifice) in the middle of a pipe. As fluid flows through the pipe and reaches the orifice, it must accelerate to pass through the smaller opening. This acceleration causes a drop in pressure, which can be measured upstream and downstream of the orifice plate.
Using Bernoulli’s equation, the flow rate can be calculated based on the pressure difference. The assumption behind this calculation is that the fluid is incompressible, steady, and has negligible viscosity.
In reality, all fluids have viscosity. As a result, energy is lost in the form of friction, especially when the flow is turbulent or when the fluid sticks to the surface of the orifice. These losses affect the pressure drop and lead to errors in flow measurement if not properly accounted for.
How Viscosity Alters Flow Behavior
When a viscous fluid passes through an orifice, it does not behave the same way as an ideal fluid. Instead of maintaining uniform velocity, the fluid experiences shear stress. This means that fluid layers move at different speeds, particularly near the pipe and orifice walls. These velocity gradients are more pronounced in high-viscosity fluids.
As the viscosity increases, the flow profile becomes more distorted. Instead of forming a clean, symmetrical jet through the orifice, the fluid may stick to the edge of the orifice and form irregular flow paths. This leads to increased energy loss and a lower pressure drop than expected for a given flow rate.
This deviation from ideal behavior causes the calculated flow rate to be inaccurate. The orifice plate flow meter assumes a certain relationship between pressure drop and flow, but viscosity changes that relationship.
Reynolds Number and Flow Regime
One of the most critical concepts in understanding the effect of viscosity on an orifice plate flow meter is the Reynolds number. This dimensionless number represents the ratio of inertial forces to viscous forces in a fluid flow. It helps classify the flow as laminar or turbulent.
In low Reynolds number conditions, flow is laminar. This is typical for high-viscosity fluids or low-velocity flows. In laminar flow, viscosity dominates, and fluid moves in smooth layers. Pressure drop behaves differently in this regime compared to turbulent flow.
In high Reynolds number conditions, flow becomes turbulent. In this regime, inertial forces dominate, and the effect of viscosity becomes less significant. Most orifice plate flow meters are calibrated assuming turbulent flow.
If the fluid has high viscosity or if the velocity is low, the Reynolds number may fall into the transitional or laminar range. In that case, the standard discharge coefficient used in the orifice flow equation may no longer be valid.
Impact on Discharge Coefficient
The discharge coefficient is a correction factor used in the flow equation for an orifice plate flow meter. It accounts for non-ideal flow effects, including friction and energy losses.
For fluids with consistent viscosity and flow conditions, the discharge coefficient can be fairly constant. However, when viscosity changes—due to temperature fluctuations or varying fluid composition—the discharge coefficient also changes.
High-viscosity fluids usually result in a lower discharge coefficient. This means that the actual flow is lower than what would be predicted using a standard equation. If the discharge coefficient is not corrected for viscosity, the flow meter will overestimate the flow rate.
Real-World Consequences of Viscosity Errors
Inaccurate flow measurements can have serious consequences in industrial settings. In chemical processing, incorrect dosage of raw materials can affect product quality. In oil pipelines, flow errors can lead to financial discrepancies. In heating and cooling systems, viscosity changes due to temperature can cause fluctuating flow measurements that compromise efficiency.
Moreover, safety concerns may arise if flow meters do not detect underflow or overflow conditions accurately. In systems involving lubrication, combustion, or reaction control, viscosity-dependent errors can cause equipment damage or process instability.
Mitigating the Impact of Viscosity
To ensure accurate readings, it is important to consider viscosity when selecting and using an orifice plate flow meter.
One solution is to perform calibration with the actual fluid under expected operating conditions. This allows the discharge coefficient to be adjusted for real viscosity effects. Another approach is to use computational models or empirical correction factors that modify the flow equation based on Reynolds number.
Some flow meters are available with software that automatically adjusts for viscosity if density and temperature sensors are integrated into the system. In some cases, alternative flow meters, such as Coriolis or positive displacement meters, may be better suited for high-viscosity fluids.
Proper installation is also crucial. Sharp-edged orifice plates, correct upstream and downstream straight pipe lengths, and smooth flow profiles help reduce the impact of viscosity.
Conclusion
The orifice plate flow meter is a reliable and time-tested device, but its performance is influenced by the physical properties of the fluid it measures. Among these properties, viscosity plays a key role.
Viscosity alters the flow profile, changes the Reynolds number, and affects the discharge coefficient. These changes can lead to inaccurate flow readings if they are not properly accounted for.
Understanding how viscosity impacts the operation of an orifice plate flow meter is essential for accurate and consistent flow measurement. By calibrating appropriately, adjusting for Reynolds effects, and installing the device correctly, engineers can mitigate the impact of viscosity and maintain confidence in their measurements.
In industrial processes where precision matters, overlooking the effect of viscosity can be costly. With thoughtful application and awareness, the orifice plate flow meter remains a powerful tool—even in challenging fluid conditions.
- Art
- Causes
- Crafts
- Dance
- Drinks
- Film
- Fitness
- Food
- Games
- Gardening
- Health
- Home
- Literature
- Music
- Networking
- Other
- Party
- Religion
- Shopping
- Sports
- Theater
- Wellness
