How Accurate is a Bourdon Pressure Gauge?
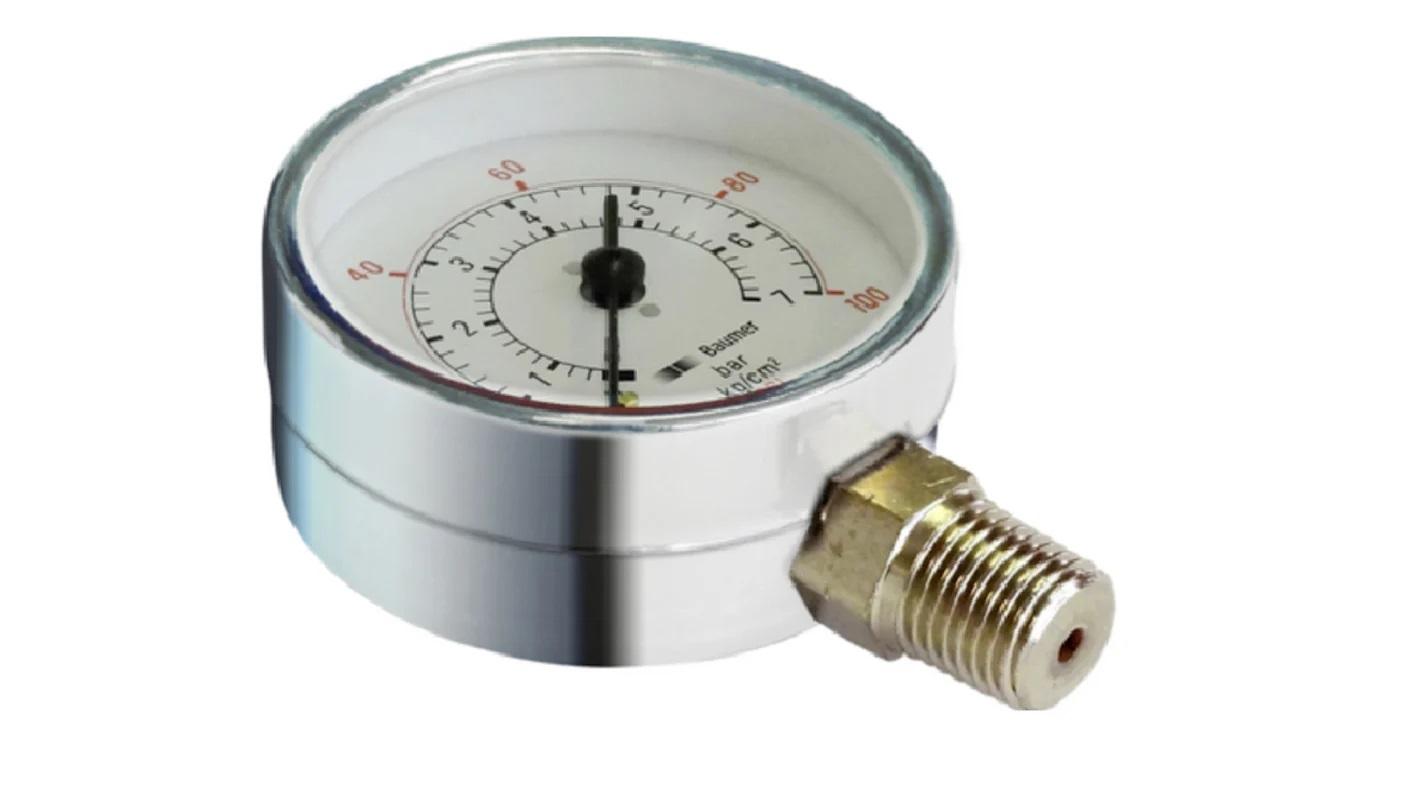
The Bourdon pressure gauge has been a fundamental instrument in pressure measurement for more than a century. Found in industries ranging from oil and gas to food processing and HVAC, this mechanical device is appreciated for its simplicity, reliability, and robustness. But one question frequently arises: How accurate is a Bourdon pressure gauge?
Understanding the accuracy of a Bourdon pressure gauge requires looking into its design, function, influencing factors, and performance standards. This article explores these aspects in depth while keeping the explanation accessible and straightforward.
What is a Bourdon Pressure Gauge?
Before assessing its accuracy, it is helpful to understand what a Bourdon pressure gauge is and how it works.
A Bourdon pressure gauge is a mechanical device that measures pressure using a curved, elastic tube called a Bourdon tube. This tube tends to straighten when pressurized. The movement of the tube’s free end is transferred to a pointer through a system of gears and levers. The pointer then displays the pressure reading on a dial.
This design is purely mechanical. It does not require power, which makes it highly dependable, especially in rugged or remote environments.
Accuracy Classifications
The accuracy of a Bourdon pressure gauge is often defined by accuracy class, a standardized metric established by organizations like ANSI (American National Standards Institute), ASME (American Society of Mechanical Engineers), and EN (European Standards).
Accuracy class is expressed as a percentage of full-scale reading. Common classes for Bourdon pressure gauges include 0.1%, 0.25%, 0.5%, 1.0%, 1.6%, and 2.5%. For example, in a gauge with a 100 psi full scale and an accuracy class of 1.0%, the permissible error is ±1 psi over the entire range.
Industrial Bourdon pressure gauges generally fall between 0.5% and 2.5% accuracy classes. Laboratory or calibration-quality gauges may achieve 0.1% or better, but such precision is not typical in regular field applications.
Factors That Affect Accuracy
While the accuracy class gives a standard baseline, real-world performance can vary due to multiple factors. Understanding these influences helps clarify how accurate a Bourdon pressure gauge will be in practice.
Temperature
Temperature changes can affect the elasticity of the Bourdon tube. Since the tube is usually made from brass, bronze, or stainless steel, thermal expansion or contraction can alter its response to pressure.
Manufacturers usually calibrate gauges at standard room temperature. In applications with extreme heat or cold, compensation may be necessary to maintain accuracy.
Vibration and Pulsation
Bourdon pressure gauges are sensitive to mechanical vibrations and pulsating pressures. These conditions can cause the pointer to oscillate or even wear out the movement mechanism over time.
To improve accuracy under such conditions, gauges may include a liquid-filled case. The liquid dampens the vibrations, which helps maintain consistent readings.
Mounting Position
The orientation of the gauge can also influence its accuracy. Most gauges are calibrated in a vertical position. When mounted at an angle or upside down, the internal components may not behave as expected, resulting in slight inaccuracies.
Age and Fatigue
Like any mechanical device, a Bourdon pressure gauge can wear out over time. The repeated flexing of the Bourdon tube leads to metal fatigue. As a result, the tube may no longer deform consistently under the same pressure, affecting the accuracy.
Routine calibration and periodic replacement are essential for maintaining reliable performance.
Overpressure and Shock
Exposing the gauge to pressures beyond its rated range can permanently deform the Bourdon tube. Once deformed, the tube can no longer return to its original shape, and the gauge loses its accuracy.
Overpressure protectors and snubbers can be used in critical applications to prevent damage.
Practical Accuracy in Field Applications
In most industrial settings, a Bourdon pressure gauge with 1.0% to 1.6% accuracy is sufficient. For example, in steam systems or hydraulic machinery, knowing the exact pressure to the decimal point is rarely necessary. What matters more is reliability and the ability to detect deviations quickly.
In such contexts, even a gauge with 2.5% accuracy can serve effectively, provided the full-scale range is appropriate. If the working pressure is 100 psi, using a gauge with a 200 psi full scale and 2.5% accuracy would yield ±5 psi deviation, which might still be acceptable depending on the process.
In contrast, processes like laboratory calibration, pharmaceutical production, or aerospace testing demand higher precision. Here, gauges with 0.1% or 0.25% accuracy are preferable, although they are more expensive and delicate.
Calibration and Verification
Accuracy is not a static quality. Over time, any Bourdon pressure gauge may drift due to wear, mechanical stress, or environmental conditions. That is why regular calibration is essential.
Calibration compares the gauge’s readings against a known pressure standard. If the readings are off, the gauge may be adjusted or replaced. In regulated industries, calibration records must be kept to comply with standards.
Frequency of calibration depends on the criticality of the application, the operating environment, and company policy. For critical operations, gauges may be checked quarterly or even monthly. In less sensitive systems, annual verification might suffice.
Enhancing Accuracy in Application
Even if a gauge is inherently limited by its class, certain best practices can enhance its effective accuracy in use.
Select a gauge with a full-scale range that is approximately twice the normal operating pressure. This ensures that the pointer stays in the middle of the scale, where readings are most accurate.
Use a gauge with a damped movement or a liquid-filled case in vibrating or pulsating environments. Always install the gauge vertically unless specified otherwise. Use snubbers or overpressure protection if pressure surges are expected.
Finally, implement a maintenance plan that includes periodic calibration and inspection.
The Bottom Line
So, how accurate is a Bourdon pressure gauge?
The answer depends on the gauge’s accuracy class, its condition, the operating environment, and how well it is maintained. In general, a well-maintained industrial Bourdon pressure gauge can offer accuracy within ±1% to ±2.5% of the full-scale range. For critical processes, more precise gauges with ±0.25% or better are available.
While not as accurate as digital pressure sensors, the Bourdon pressure gauge offers a dependable, cost-effective, and power-free way to monitor pressure. With proper selection and maintenance, it can provide sufficiently accurate readings for a wide range of industrial and mechanical systems.
Conclusion
The Bourdon pressure gauge remains one of the most trusted tools in pressure measurement. Its accuracy, while dependent on several factors, is more than adequate for the vast majority of applications. Understanding how it works and what influences its performance helps ensure it is used to its fullest potential.
In a world increasingly dominated by digital technology, the humble Bourdon pressure gauge continues to prove that precision and simplicity can go hand in hand.
- Art
- Causes
- Crafts
- Dance
- Drinks
- Film
- Fitness
- Food
- Игры
- Gardening
- Health
- Главная
- Literature
- Music
- Networking
- Другое
- Party
- Religion
- Shopping
- Sports
- Theater
- Wellness
