Why is an industrial laser cleaner often preferred over traditional abrasive methods in factories?
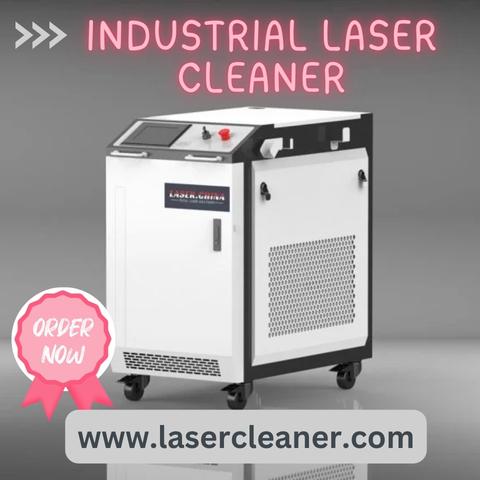
In modern manufacturing and heavy industries, surface preparation and cleaning have always been critical tasks. Whether it’s removing paint, rust, oil, oxide layers, or production residues, achieving a clean surface is vital for maintaining equipment, improving bonding, or preparing for finishing processes. Historically, factories have relied on sandblasting, chemical treatments, and manual scrubbing to handle these tasks. However, in recent years, the industrial laser cleaner has quietly disrupted these long-standing methods.
This shift is not random or hype-driven. It's grounded in operational needs, safety requirements, and the increasing demand for high-precision, low-waste, and scalable cleaning methods. So when factory managers and industrial engineers ask why this tool is now preferred, the answer lies in how it changes the cleaning game at its core.
How Industrial Laser Cleaning Works
The industrial laser cleaner uses a focused laser beam to irradiate the surface of a material. When this beam interacts with contaminants like rust, oxides, grease, or paint, the energy is absorbed selectively by the unwanted layer. This sudden energy absorption leads to the rapid heating, expansion, and vaporization or detachment of the contaminant — without affecting the underlying material.
The process is controlled, non-contact, and localized. It doesn't require any chemical agents or blast media. What’s left behind is a bare surface that’s often more ready for bonding, coating, or welding than those cleaned using conventional methods.
Cleaning in High-Stakes Environments
Consider an aerospace maintenance workshop dealing with complex components made from titanium or carbon fiber. These parts require cleaning before inspection or reassembly. Traditional methods could introduce micro-abrasions or leave chemical residues. The industrial laser cleaner, however, removes only the contamination layer, maintaining the substrate integrity. It’s especially important in aerospace, where surface damage could lead to catastrophic failure in service.
Similarly, in the energy sector — from wind turbines to nuclear reactors — surface coatings, corrosion, and buildup are regular issues. Here, downtime is expensive and worker safety is paramount. The laser system can be automated or integrated with robotic arms to clean large, hard-to-access surfaces without exposing workers to hazardous dust or chemicals.
Productivity Without the Mess
One silent problem with traditional cleaning methods is the secondary mess they create. Sandblasting leaves behind grit. Chemical stripping introduces liquid waste, requiring disposal under strict environmental rules. Manual grinding or wire brushing creates dust and scrap particles that require cleanup and filtration.
With the industrial laser cleaner, this problem is minimized. Most laser cleaning operations create only a fine dust or vaporized residue, which is easily captured with a standard filtration system or vacuum. For factory owners and maintenance teams, this reduces the need for post-cleaning cleanup, minimizes machine downtime, and improves operational efficiency.
Non-Destructive by Nature
When cleaning engine blocks, aerospace fasteners, high-precision molds, or electrical components, preserving the base material is critical. Abrasive techniques remove layers indiscriminately, sometimes thinning or damaging parts. In contrast, laser cleaning operates with surgical precision. The user can dial in the exact wavelength, pulse duration, and power needed to affect only the unwanted layer.
This level of control is one of the main reasons the industrial laser cleaner is now a trusted tool in industries where part integrity cannot be compromised — such as defense manufacturing, automotive production lines, and electronics.
Repeatability for Mass Production
In a factory setting, anything that can be automated and repeated consistently earns high value. Manual techniques, regardless of how skilled the operator is, introduce variability. One part might be cleaned thoroughly, another might retain residue in corners or edges. Over time, this inconsistency affects downstream processes such as coating adhesion or welding strength.
An industrial laser cleaner can be mounted on an automated gantry or integrated with a robotic arm. Once the cleaning parameters are programmed, every part receives the same treatment — line after line, shift after shift. This is a major advantage in industries where standardization and traceability are mandatory.
Safe Operation with the Right Setup
While the word “laser” may sound hazardous, industrial laser cleaning systems are designed with operator safety in mind. Enclosed systems, proper shielding, interlocks, and training all contribute to making laser cleaning one of the safer industrial cleaning options.
For instance, chemical-based cleaning exposes workers to solvents, acids, or volatile organic compounds (VOCs), while abrasive blasting requires full-body protection to avoid inhaling dust or debris. Laser systems remove these hazards from the equation — especially in enclosed or automated setups.
Minimal Environmental Impact
Environmental regulations are tightening globally, with companies under increasing pressure to minimize waste, emissions, and hazardous materials. The industrial laser cleaner naturally aligns with these goals. It doesn’t use consumables, doesn’t produce chemical runoff, and generates only small amounts of particulate waste.
For industries operating under ISO 14001 environmental management standards or similar certifications, switching to laser cleaning contributes directly to sustainability goals without compromising cleaning performance.
Cleaning Complex Surfaces
Some machine parts or tools have grooves, curved surfaces, or hard-to-reach areas. Traditional cleaning methods often struggle in these zones. Brushes miss corners. Sandblasting may overdo flat areas and miss indents. Chemicals don’t flow evenly and require soaking time.
Laser beams, however, can be focused into small, agile paths that follow any geometry — even on small or detailed parts. An industrial laser cleaner with a 3D scanner or robotic nozzle can navigate complex surface profiles with consistent results, something that is highly valuable for precision mold maintenance or tool refurbishment.
Cost Predictability Over Time
A common concern with introducing new equipment is cost unpredictability. With many cleaning methods, there are recurring costs: media for sandblasting, disposal of hazardous waste, buying chemical agents, or replacing worn tools. Over time, these add up and fluctuate with market conditions.
The industrial laser cleaner, once purchased, has a predictable operating cost. Electricity, minor maintenance, and the occasional replacement of optical parts are the primary concerns. There's no ongoing purchase of consumables, and downtime for maintenance is minimal. For factories looking to streamline operational budgeting, this makes laser cleaning attractive.
Versatility Across Industries
Laser cleaning isn’t restricted to one niche. It has found its way into automotive factories for paint removal before welding, into railway workshops for maintenance of rolling stock, and into electronics for oxide removal before soldering. Even food processing equipment can benefit from laser decontamination in stainless steel setups.
This broad versatility allows a single system to serve multiple departments within a facility. For example, a large manufacturing plant can use the same industrial laser cleaner for cleaning welding jigs, removing coating buildup on machinery, and preparing parts for surface inspection.
Final Thoughts
The industrial landscape is evolving, and so are the tools needed to support cleaner, faster, and more sustainable operations. The industrial laser cleaner stands out not as a flashy trend, but as a practical solution to real-world challenges. Its ability to deliver precision, reduce waste, operate safely, and adapt to diverse cleaning tasks makes it a strong choice for industries serious about long-term efficiency and quality control. As manufacturing continues to embrace automation and high-performance standards, this technology is becoming less of an option — and more of a necessity.
- Art
- Causes
- Crafts
- Dance
- Drinks
- Film
- Fitness
- Food
- Jogos
- Gardening
- Health
- Início
- Literature
- Music
- Networking
- Outro
- Party
- Religion
- Shopping
- Sports
- Theater
- Wellness
