Elevate Welding Outcomes through Supplier Data Integration
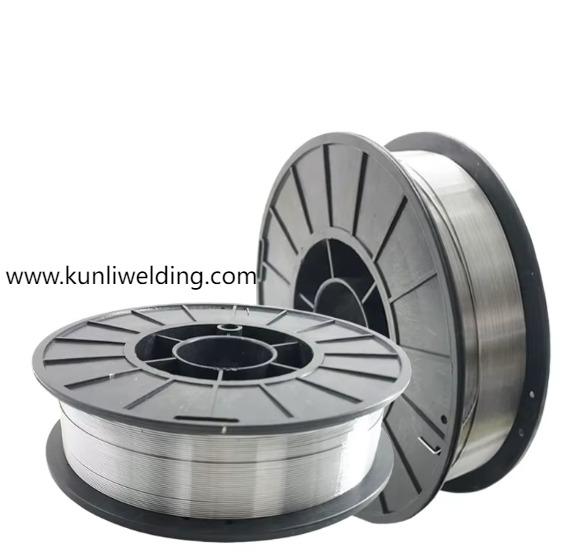
When fabricators compare filler options, understanding how Aluminum Tig Wire Suppliers differ from MIG providers is essential for achieving precise welds in cutting-edge projects. As industries accelerate the rollout of electric vehicle platforms and modernize power distribution networks, the choice between TIG and MIG wire influences both production efficiency and joint integrity. By examining sourcing practices and technical support offerings, professionals can align welding strategies with evolving fabrication demands.
TIG wire sourcing emphasizes alloy purity and tight diameter tolerances. Suppliers that invest in clean melting processes and continuous casting deliver rods that feed smoothly in pulsed current applications. In contrast, MIG wire partners often focus on spool convenience and consistent alloy chemistry across large coil volumes. While MIG wire suits high-speed deposition in automated lines, TIG runners enhance control over heat input, making them ideal for thin sections or aesthetic weld seams. Recognizing these distinctions steers teams toward the right wire type and supplier relationship.
Sustainability has emerged as a driving factor in supply decisions. As renewable energy farms expand and offshore structures rely on corrosion-resistant joints, TIG wire producers integrate recycled aluminum content under strict trace systems. Meanwhile MIG wire sources may prioritize logistics efficiency to maintain steady inventory levels amid global material fluctuations. Fabricators targeting green benchmarks benefit from transparent supply chains that verify recycled inputs and document energy-saving measures in melting and extrusion stages.
Technical collaboration varies between wire types. TIG wire specialists typically offer tailored consultation on bead shaping and arc stability under varied shielding gas conditions. They may provide custom spool packaging to minimize oxidation during storage and protect fine diameters from damage. MIG wire distributors often supply comprehensive feeder kits and nozzle maintenance guides to support uninterrupted high-volume operations. Evaluating after-sales responsiveness and training programs ensures weld teams maximize uptime and quality, regardless of chosen process.
Packaging and shipping solutions further distinguish providers. TIG wire arrives in sealed containers designed to preserve surface cleanliness and prevent moisture pickup in humid climates. Suppliers handling MIG coils focus on robust reels that integrate smoothly with pull-push feeders and automated handling systems. Those managing both product lines must adapt packaging formats to protect wire integrity from warehouse to workbench, supporting reactive project timelines.
Current market chatter around infrastructure upgrades highlights the importance of weld repeatability. Whether joining thin panels in advanced vehicle chassis or splicing busbars in substation retrofits, the ability to reproduce weld profiles consistently depends on wire consistency and supplier guidance. Expert Aluminum Tig Wire Suppliers often conduct on-site sampling sessions, fine-tuning amperage recommendations and travel speeds. MIG wire vendors may offer remote monitoring dashboards that track feed speed and voltage stability to preempt interruptions.
Cost considerations extend beyond per-unit pricing. TIG wire sourcing requires evaluating scrap rates and cleaning processes needed for post-weld finishing. Suppliers that supply oxygen-free packaging and detailed handling instructions help reduce rework and surface touch-up. Conversely, MIG wire contracts often include volume-based logistics discounts and flexible replenishment schedules to mitigate stock-out risks. Balancing these factors against project complexity informs a comprehensive procurement strategy.
As digital fabrication hubs embrace Industry automation standards, wire suppliers integrate sensor-based quality controls in extrusion lines. TIG rod producers scan each length for diameter variance and surface anomalies, while MIG coil manufacturers log spool run-out metrics. These data-driven approaches support traceability and continuous improvement initiatives, key for projects that demand certification and audit trails.
Choosing the right welding wire partner means aligning technical strengths with project objectives and sustainability goals. By comparing how TIG and MIG suppliers manage alloy sourcing, packaging, support, and data integration, fabrication teams can secure reliable materials for demanding applications. To explore alloy options and discuss tailored wire solutions from Kunliwelding, visit www.kunliwelding.com/product/ where detailed product profiles and expert guidance await proactive weld professionals.
- Art
- Causes
- Crafts
- Dance
- Drinks
- Film
- Fitness
- Food
- Giochi
- Gardening
- Health
- Home
- Literature
- Musica
- Networking
- Altre informazioni
- Party
- Religion
- Shopping
- Sports
- Theater
- Wellness
