The Impact of Production Techniques on the Leak Resistance of Plastic Water Bottles
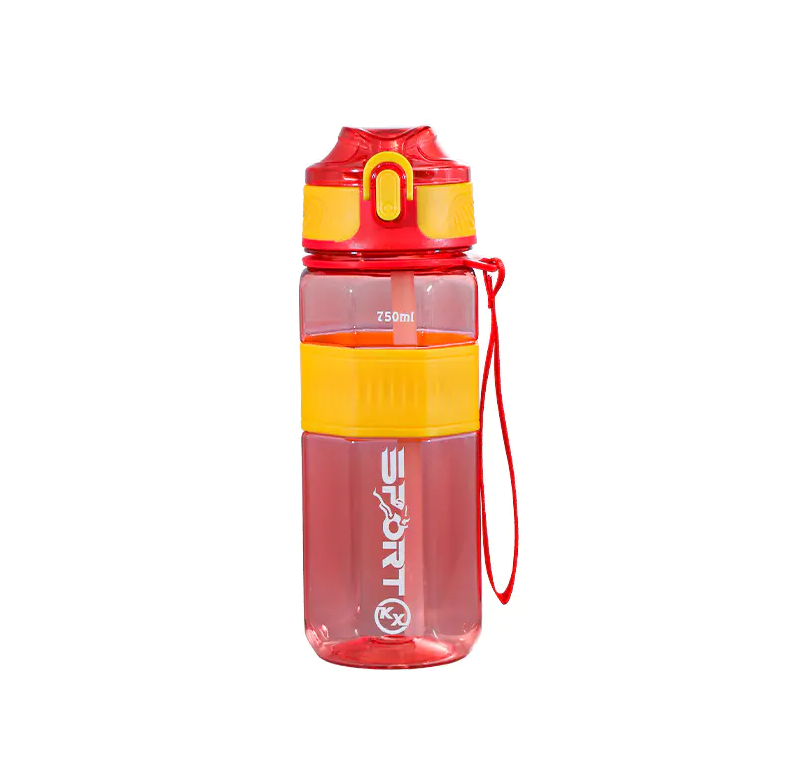
Leak proof plastic water bottles have become indispensable in daily life, prized for their portability and spill-free design. However, beyond material choice, the manufacturing process plays a crucial role in determining the bottle’s leak-proof performance. This article explores how production techniques impact the reliability of leak proof plastic water bottles and what factors manufacturers must control to ensure optimal sealing.
Injection Molding and Precision
Most plastic water bottles are produced through injection molding, a process where molten plastic is injected into a mold cavity to form the bottle’s body and components. The precision of this process is vital; even slight imperfections in mold design or injection parameters can lead to misalignments or weak points.
For a leak proof bottle, accuracy in shaping the bottle neck and threading is essential. The cap must mate perfectly with the neck to form a tight seal, so production tolerances must be tightly controlled to avoid gaps that cause leaks.
Seal Integration and Material Compatibility
The leak proof feature largely depends on the gasket or seal material, often silicone or rubber, which is fitted inside the cap. The production process must ensure proper integration of the seal with the plastic cap.
If the seal is poorly attached or the materials are incompatible, separation can occur during use, resulting in leakage. Manufacturing processes such as ultrasonic welding or adhesive bonding are often used to secure seals, and their quality directly affects the leak resistance.
Quality Control and Testing
Stringent quality control measures during production help maintain consistent leak proof performance. Bottles are typically tested for leaks under pressure or tilt to simulate real-world conditions.
Manufacturers using automated inspection systems can detect defects like malformed threads, incomplete seals, or surface irregularities early. Without such control, defective units may reach consumers, undermining trust in the product.
Impact of Production Scale and Cost
Large-scale production can sometimes pressure manufacturers to prioritize speed over quality, increasing the risk of defects affecting leak proof performance. Conversely, smaller batch production often allows more attention to detail and stricter process monitoring.
Choosing the right balance between cost efficiency and production quality is critical. High-quality leak proof plastic water bottles often reflect this in their price, as better manufacturing processes incur higher costs.
Innovations in Manufacturing
Recent advances in production technology, such as 3D mold printing and precision robotics, enable manufacturers to create bottles with highly consistent and complex features that improve sealing.
Additionally, improvements in seal materials and bonding techniques contribute to better durability and leak proof reliability.
Conclusion
The production process significantly influences the leak proof performance of plastic water bottles. From the precision of molding the bottle neck and threads to the secure integration of sealing materials, manufacturing quality is a key factor.
Consumers looking for reliable leak proof plastic water bottles should consider not only the material but also the brand’s reputation for manufacturing quality and testing rigor. Properly manufactured bottles provide peace of mind that spills and leaks will be minimized in daily use.
- Art
- Causes
- Crafts
- Dance
- Drinks
- Film
- Fitness
- Food
- Jogos
- Gardening
- Health
- Início
- Literature
- Music
- Networking
- Outro
- Party
- Religion
- Shopping
- Sports
- Theater
- Wellness
