How Automatic Feeding Functions Are Realized in Horizontal Band Saw Machine Technology
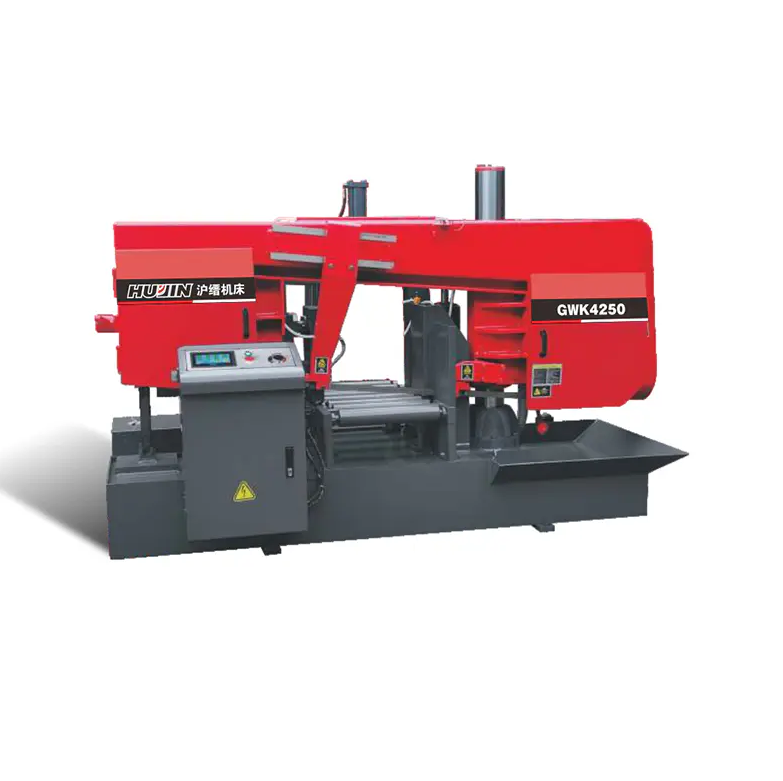
The automatic feeding function of a Horizontal Band Saw Machine is a vital feature that greatly enhances production efficiency, consistency, and operator convenience. By automating the process of advancing the workpiece into the cutting zone, the machine reduces manual handling, speeds up the cutting cycle, and allows for more precise and repeatable cuts. This function is typically realized through a combination of mechanical components, sensors, and control systems that work together to manage material movement in a synchronized and reliable manner.
At its core, the automatic feeding system in a Horizontal Band Saw Machine consists of a feed mechanism that controls how the workpiece is pushed or pulled toward the saw blade. This mechanism often includes a feed carriage or clamp that securely grips the material to ensure stable movement without slippage. The carriage is driven by either hydraulic cylinders, pneumatic actuators, or electric motors, depending on the machine’s design and intended application. Hydraulic feed systems are common in heavier-duty machines due to their power and smooth motion, while electric drives offer precise control and easier integration with computerized controls.
The feeding speed and stroke length are usually adjustable to accommodate different material sizes and cutting requirements. Sensors or position encoders monitor the carriage’s movement and send feedback to the machine’s control unit, which in turn regulates the feed rate to optimize cutting conditions. This precise control helps prevent overfeeding that could overload the saw blade or underfeeding that would reduce productivity.
In more advanced Horizontal Band Saw Machines, programmable logic controllers (PLCs) or CNC systems govern the entire feeding operation. These controllers allow operators to set parameters such as cut length, feed speed, and number of cuts. Once programmed, the automatic feed system executes these commands with minimal human intervention, resulting in consistent and repeatable cuts. This automation is especially valuable in batch production environments where multiple identical parts are needed.
Another important aspect of the automatic feeding function is the integration of safety features. The system often includes sensors that detect if the material is properly clamped or if there is any obstruction along the feed path. If an issue is detected, the feeding process halts immediately to prevent damage to the machine or injury to the operator. Additionally, emergency stop controls and manual override options are typically provided to ensure full operational safety.
The effectiveness of the automatic feeding function also depends on the design of the material support system. Roller conveyors, ball transfers, or roller beds are commonly installed in conjunction with the feeding carriage to facilitate smooth material movement into and out of the cutting area. Proper alignment and support prevent material sagging or jamming, which could interfere with the feeding cycle and compromise cutting accuracy.
Overall, the automatic feeding feature in a Horizontal Band Saw Machine is a sophisticated integration of mechanical drives, sensors, and programmable control technology. This synergy not only boosts production efficiency but also improves cut quality by maintaining steady, controlled material movement. For industries requiring high throughput and precision, the automatic feed function is an indispensable aspect of modern Horizontal Band Saw Machine design.
- Art
- Causes
- Crafts
- Dance
- Drinks
- Film
- Fitness
- Food
- الألعاب
- Gardening
- Health
- الرئيسية
- Literature
- Music
- Networking
- أخرى
- Party
- Religion
- Shopping
- Sports
- Theater
- Wellness