Exploring the Operational Principles and Industrial Applications of a Roller Granulator Machine
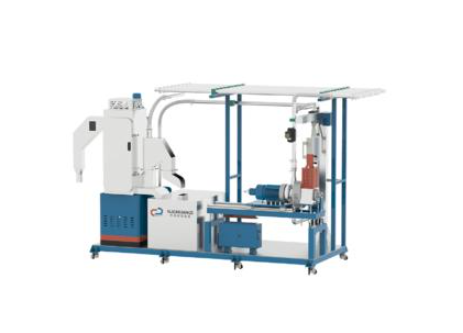
A roller granulator is a critical piece of equipment widely used in the fertilizer, chemical, and pharmaceutical industries to produce uniform granules from powders or powders mixed with binders. Its efficient granulation process is essential for creating high-quality products that are easy to handle, transport, and apply. Understanding how a roller granulator operates and its benefits can help industries optimize production processes and improve product consistency.
The fundamental working principle of a roller granulator involves compressing raw materials between two counter-rotating rollers to form compacted sheets or flakes. These sheets are then broken down into granules of desired sizes. The rollers’ pressure and speed can be adjusted to control the density and size distribution of the granules, ensuring uniformity and optimal physical properties. This mechanical granulation process is energy-efficient and produces minimal dust compared to other methods.
One of the main advantages of using a roller granulator is its ability to handle a wide range of raw materials, including organic and inorganic powders. This versatility makes it popular in fertilizer manufacturing, where consistent granule size affects the product’s dissolution rate and nutrient release. Additionally, the granulator’s compact design and relatively simple operation make it suitable for both small and large-scale production facilities.
In addition to efficient granule formation, roller granulators offer improved product quality. The compacted granules typically exhibit higher strength and lower friability, meaning they are less prone to breaking apart during handling and transportation. This enhances shelf life and ensures uniform application in agricultural or industrial settings.
Maintenance is key to ensuring the roller granulator’s longevity and optimal performance. Regular inspection of the rollers for wear, timely replacement of worn parts, and proper lubrication of moving components prevent downtime and costly repairs. Cleaning the machine after each production cycle is also important to avoid contamination and buildup of residual materials.
Despite its many benefits, a roller granulator may not be suitable for materials that are extremely fine, sticky, or moisture-sensitive without prior treatment or the addition of suitable binders. Operators should carefully evaluate material characteristics and process parameters to achieve the best results.
In conclusion, a roller granulator is an essential machine for producing high-quality granules across various industries. Its efficient mechanical process, adaptability to different materials, and ability to improve product strength make it a valuable investment for manufacturers. Proper maintenance and operation further enhance its reliability and output consistency.
- Art
- Causes
- Crafts
- Dance
- Drinks
- Film
- Fitness
- Food
- Giochi
- Gardening
- Health
- Home
- Literature
- Musica
- Networking
- Altre informazioni
- Party
- Religion
- Shopping
- Sports
- Theater
- Wellness
