How Accurate Is a Bourdon Pressure Gauge?
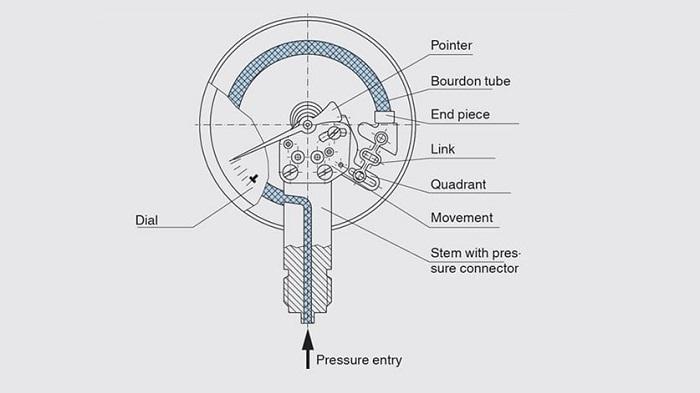
Pressure measurement is vital in many industrial, mechanical, and scientific applications. One of the oldest and most widely used devices for measuring pressure is the Bourdon pressure gauge. Named after its inventor Eugène Bourdon in the mid-19th century, this device has become a trusted tool in workshops, factories, laboratories, and processing plants.
The Bourdon gauge is known for its simplicity, durability, and versatility. It operates without electricity, making it ideal for remote or hazardous environments. Its mechanical design converts pressure into needle movement, giving users a direct and readable indication of fluid or gas pressure.
But how accurate is a Bourdon pressure gauge? This article will explore the structure of the Bourdon gauge, the factors that affect its accuracy, how its accuracy compares to other devices, and the best practices for using it reliably. Understanding its strengths and limits will help engineers and technicians apply it effectively in the field.
How the Bourdon Pressure Gauge Works
The Bourdon pressure gauge works through the elastic deformation of a curved, hollow metal tube. When pressure is applied inside the tube, it tries to straighten out. This motion is transferred through a mechanical linkage to a pointer on a dial face.
As the pressure increases, the tube expands slightly. As the pressure decreases, it returns to its original shape. The movement is small, but the mechanical linkage amplifies it and turns it into a circular motion. This movement rotates the needle, indicating the pressure level on a calibrated scale.
The simplicity of the Bourdon mechanism is one of its greatest strengths. It contains few moving parts, and all of them are mechanical. This makes the gauge robust, especially in environments where digital or electronic sensors might fail due to heat, moisture, or shock.
Standard Accuracy Ranges
The accuracy of a Bourdon pressure gauge depends on its design, quality, and intended use. Manufacturers classify gauges into accuracy grades, which are expressed as a percentage of full-scale reading.
For general industrial use, a common accuracy is ±1.6 percent of full-scale. This means that if a gauge has a range of 0 to 100 psi, the actual pressure could be 1.6 psi above or below the reading shown by the pointer. For example, if the needle points to 50 psi, the actual pressure could be anywhere between 48.4 and 51.6 psi.
For more precise applications, such as laboratory or calibration work, Bourdon gauges with an accuracy of ±0.25 or ±0.5 percent are available. These higher-accuracy models are more expensive and are built with better materials, tighter tolerances, and more precise assembly.
Lower-grade gauges may have an accuracy of ±2 or ±3 percent, which is sufficient for non-critical applications such as monitoring tire pressure or checking hydraulic tools.
Factors That Affect Accuracy
Several factors can influence the accuracy of a Bourdon pressure gauge. These include design, environment, usage, and maintenance. While the core mechanism is reliable, external conditions can introduce small errors or mechanical wear over time.
The quality of materials used in the Bourdon tube and linkages directly affects accuracy. Stainless steel or phosphor bronze tubes provide better consistency and resistance to fatigue. Low-cost materials may deform more over time, reducing repeatability and accuracy.
Temperature also affects gauge accuracy. Extreme heat or cold can cause the Bourdon tube to expand or contract, changing the calibration. For this reason, many gauges include a temperature compensation scale or are built to operate within a specific temperature range.
Vibration is another challenge. In environments with heavy machinery, constant vibration can cause the pointer to oscillate or even loosen internal components. This leads to erratic readings. To avoid this, liquid-filled Bourdon gauges are often used. The liquid dampens the movement and protects the mechanism.
Pressure spikes or overpressure conditions can permanently deform the Bourdon tube. Once deformed, it cannot return to its original shape and will give false readings. Some gauges include a pressure relief mechanism or overpressure stops to protect against such events.
Improper installation or misalignment can also reduce accuracy. If the gauge is mounted at an angle, the weight of the pointer and friction in the linkage can affect movement. Manufacturers recommend mounting the gauge in a vertical position at eye level.
Calibration and Testing
To ensure accurate readings, Bourdon pressure gauges should be calibrated regularly. Calibration involves comparing the gauge reading to a reference pressure source and adjusting the needle if needed. The reference source should be more accurate than the gauge being tested.
Routine calibration helps catch drift or wear before it becomes significant. Many industries follow schedules for checking gauges, especially in regulated sectors like pharmaceuticals, energy, and aviation.
Portable pressure calibrators and dead-weight testers are commonly used for this purpose. Some facilities also use automated calibration benches for high-volume testing.
If a gauge fails calibration by a large margin, it should be removed and either repaired or replaced. In most cases, the problem lies in worn or deformed components inside the gauge.
Comparison to Other Pressure Devices
Compared to modern digital pressure sensors, the Bourdon gauge is less accurate. Digital sensors can offer precision within 0.1 percent or better, along with temperature correction and remote monitoring. However, these devices need power and are more sensitive to environment and contamination.
The Bourdon gauge is better suited to harsh or remote areas where electricity is not available. It also gives a quick visual reference without needing a screen or software.
In pneumatic and hydraulic systems, Bourdon gauges remain the most commonly used mechanical instrument. They are especially useful during maintenance checks and field inspections.
Practical Use and Best Practices
To get the best accuracy from a Bourdon pressure gauge, it is important to choose the right gauge for the job. The pressure range should be selected so that normal operating pressure falls within the middle third of the scale. This reduces the effect of scale errors at the low and high ends.
Regular inspections help detect signs of wear, corrosion, or damage. A slow needle response or flickering may indicate internal problems. Discoloration or leaks inside a liquid-filled case also signal a need for service.
Using snubbers or pulsation dampeners in high-vibration systems can protect the gauge. These accessories reduce pressure spikes and mechanical stress on the Bourdon tube.
Replacing gauges at regular intervals, especially in safety-critical systems, helps maintain overall process reliability. Always store spare gauges in clean, dry environments to prevent degradation.
Conclusion
The Bourdon pressure gauge is a time-tested tool in the world of mechanical engineering. Its design may be over a century old, but it continues to offer practical value across many industries. Its accuracy is more than sufficient for most industrial and mechanical applications when used correctly.
While digital sensors offer higher precision, the Bourdon gauge provides unmatched simplicity, ruggedness, and reliability. Understanding how it works and what affects its accuracy allows engineers and technicians to apply it with confidence.
In clean, controlled conditions with proper installation and regular calibration, a Bourdon pressure gauge can maintain accuracy within one percent of full scale. In less demanding environments, even lower-grade models provide useful and dependable readings. It remains a cornerstone of mechanical pressure measurement today.
- Art
- Causes
- Crafts
- Dance
- Drinks
- Film
- Fitness
- Food
- الألعاب
- Gardening
- Health
- الرئيسية
- Literature
- Music
- Networking
- أخرى
- Party
- Religion
- Shopping
- Sports
- Theater
- Wellness