What Device Do Digital Pressure Gauges Use to Operate?
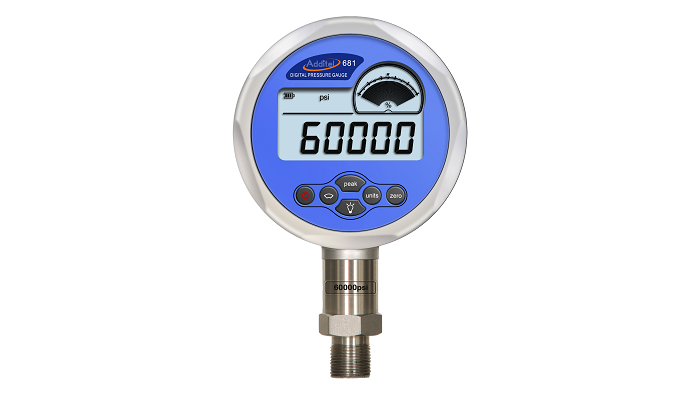
Digital pressure gauges are essential tools in modern engineering and industrial systems. They measure pressure and display it in a digital format. Unlike analog pressure gauges, digital models offer high accuracy and ease of reading. These devices are widely used in sectors such as oil and gas, HVAC, water treatment, aerospace, and manufacturing. Their importance is due to their ability to deliver real-time pressure data that can be easily read and monitored.
At the heart of every digital pressure gauge lies a sensing device. This is the key component that detects pressure and converts it into an electrical signal. Without this device, a digital pressure gauge would not function. The choice of sensing technology depends on the application, the environment, and the level of precision needed. In this article, we will explore the specific devices that digital pressure gauges use to operate, how they work, and why they are important in the broader context of measurement and control.
The Pressure Sensor as the Core Device
The main device that digital pressure gauges use to operate is a pressure sensor. A pressure sensor is a transducer that converts applied pressure into an electrical signal. This electrical signal is then interpreted by the internal electronics of the gauge and displayed on the screen as a readable pressure value.
Pressure sensors can detect pressure changes in gases, liquids, and even vapors. Their role is to measure the force exerted by the medium per unit area. The output they produce is typically a small voltage or current signal, which the microprocessor inside the digital pressure gauge processes.
There are different types of pressure sensors based on the principle they use. These include strain gauge sensors, piezoresistive sensors, capacitive sensors, and piezoelectric sensors. Each type has its own strengths and weaknesses, but all serve the same purpose—to detect pressure and provide data to the digital display.
How Strain Gauge Sensors Work
One of the most common devices used in digital pressure gauges is the strain gauge sensor. This sensor operates based on the principle of deformation. When pressure is applied to a diaphragm inside the sensor, it causes the diaphragm to flex slightly. Bonded to this diaphragm are small strain gauges, which are thin pieces of wire or foil that also deform with the diaphragm.
As the strain gauges change shape, their electrical resistance also changes. This change in resistance is directly related to the amount of pressure applied. An electrical circuit inside the gauge detects the resistance change and converts it into a voltage signal. The digital electronics then interpret this signal and display the corresponding pressure value on the screen.
Strain gauge sensors are highly accurate and stable. They are ideal for use in industrial settings where conditions may vary. Their robustness and repeatability make them one of the most reliable devices in digital pressure measurement.
Piezoresistive Sensors in Digital Gauges
Another widely used device in digital pressure gauges is the piezoresistive sensor. These sensors also rely on the relationship between mechanical stress and electrical resistance. However, instead of using metal strain gauges, they use semiconductor materials such as silicon. These materials are more sensitive to deformation, which allows the sensor to detect even very small pressure changes.
When pressure is applied to the diaphragm of a piezoresistive sensor, it causes a change in the resistance of the semiconductor elements. This resistance change generates an electrical signal that is proportional to the pressure applied. The signal is then sent to the microprocessor of the digital pressure gauge, which converts it into a readable number.
Piezoresistive sensors are favored for their high sensitivity and low cost. They are used in medical equipment, portable devices, and other applications where compact size and fast response time are essential. They are not as rugged as strain gauge sensors, but their performance is excellent for moderate operating conditions.
Capacitive Pressure Sensors
Capacitive pressure sensors work on a different principle. They use changes in electrical capacitance to measure pressure. The basic design includes two parallel plates—one fixed and one flexible. The space between these plates forms a capacitor. When pressure is applied, the flexible plate moves, changing the distance between the plates and, therefore, the capacitance.
This change in capacitance is detected by the internal electronics and converted into a signal that reflects the pressure level. Capacitive sensors can detect very small changes in pressure with great accuracy. They are often used in clean environments such as laboratories and semiconductor manufacturing.
Digital pressure gauges that use capacitive sensors are known for their sensitivity and long-term stability. They are less common than strain gauge and piezoresistive types but are essential in situations that demand high precision.
Piezoelectric Sensors for Dynamic Pressure
In applications where pressure changes rapidly and needs to be tracked in real time, piezoelectric sensors are often used. These sensors generate an electrical charge when pressure is applied. The materials used in piezoelectric sensors, such as quartz or ceramic, produce electricity in response to mechanical force.
Because piezoelectric sensors generate their own electrical signal, they do not require an external power supply. This makes them suitable for high-speed data collection and dynamic pressure monitoring. However, they are not suitable for static pressure measurements because they cannot maintain a signal for long periods.
Digital pressure gauges with piezoelectric sensors are used in engines, combustion systems, and other fast-moving environments. Their ability to respond instantly makes them ideal for research and diagnostics.
Electronics and Display System
The pressure sensor is only one part of the digital pressure gauge. Once the sensor generates an electrical signal, it must be processed. Inside the gauge, a microcontroller receives the signal. It converts the raw data into a pressure value using calibration information stored in memory. The final number is then shown on the digital screen.
The display may show pressure in different units such as psi, bar, kPa, or MPa. Many digital pressure gauges also include functions like zero reset, peak pressure memory, and alarms. These features improve usability and make digital gauges more flexible than their analog counterparts.
The electronics also include a power source, usually a battery, and in some cases, communication ports. Some digital pressure gauges can transmit data wirelessly or through wired connections. This makes them useful in automation systems and remote monitoring setups.
Final Thoughts
Digital pressure gauges rely on advanced sensing technology to function. At the core of each device is a pressure sensor that converts physical pressure into an electrical signal. This sensor can be based on strain gauge, piezoresistive, capacitive, or piezoelectric technology. Each type has specific advantages depending on the application.
Digital pressure gauges also include sophisticated electronics that interpret the signal and present the pressure reading in a clear, accurate format. Their ability to offer precision, durability, and real-time monitoring has made them the standard in many industries.
Understanding what device a digital pressure gauge uses to operate helps engineers and technicians select the right tool for the job. Whether working in a laboratory, a factory, or a hospital, the choice of sensor technology ensures that the gauge performs reliably and accurately under all conditions.
- Art
- Causes
- Crafts
- Dance
- Drinks
- Film
- Fitness
- Food
- الألعاب
- Gardening
- Health
- الرئيسية
- Literature
- Music
- Networking
- أخرى
- Party
- Religion
- Shopping
- Sports
- Theater
- Wellness