What Are the Tolerances Achievable With CNC Machining for Brass?
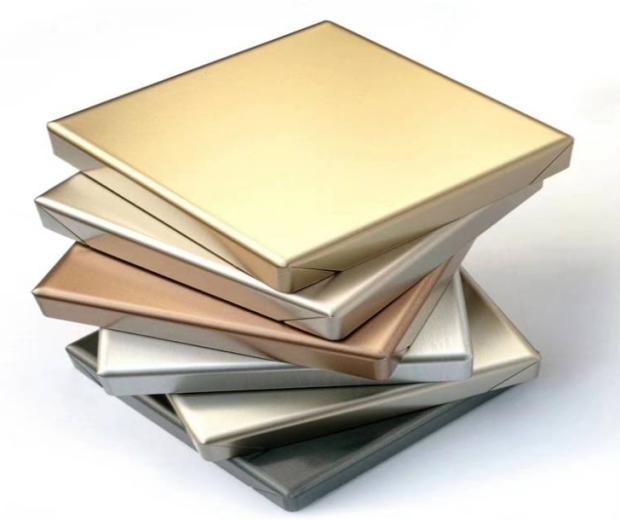
The tolerances achievable with CNC machining for brass depend on several factors, but typically range from ±0.002 inches (0.05 mm) to ±0.005 inches (0.013 mm). Here's a breakdown of what influences tolerance in CNC machining of brass:
l Machine Capability: The precision of the CNC machine itself plays a major role. High-end machines with advanced control systems and rigid construction can achieve tighter tolerances compared to basic machines.
l Tooling Selection: The type and size of cutting tools used can impact tolerance. Smaller, sharper tools can achieve finer details and tighter tolerances, while larger tools might be limited in their ability to precisely remove material.
l Machining Operation: Certain machining operations inherently offer better tolerance capabilities. Milling, for example, can generally achieve tighter tolerances than drilling or turning on a lathe.
l Material Properties: The specific brass alloy being machined can influence tolerance. Some brass alloys are more free-machining (easier to cut cleanly) than others. This can affect the consistency of the machined surface and potentially impact tolerance.
l Part Geometry: The complexity of the part design can influence achievable tolerances. Simpler geometries with larger features are easier to machine precisely compared to parts with intricate details or thin walls.
l Post-Machining Processes: In some cases, tolerances can be improved through secondary processes like grinding, polishing, or EDM (Electrical Discharge Machining) after the initial CNC machining. However, these add extra steps and cost.
It's important to discuss tolerance requirements with your CNC machining service provider. They can assess your specific part design and desired outcome to recommend achievable tolerances and potential costs involved.
- Art
- Causes
- Crafts
- Dance
- Drinks
- Film
- Fitness
- Food
- Giochi
- Gardening
- Health
- Home
- Literature
- Musica
- Networking
- Altre informazioni
- Party
- Religion
- Shopping
- Sports
- Theater
- Wellness
