Introducing Molded Plastic Components: Ensuring Durability and Reliability
Posted 2024-03-18 02:43:51
0
6K
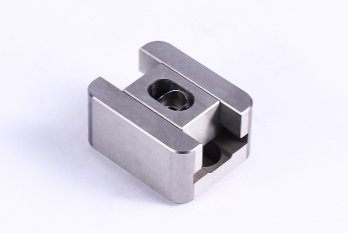
In today's market, molded plastic components stand out as indispensable elements in various industries, owing to their robustness and longevity. These components play a pivotal role in enhancing the functionality and performance of countless products, spanning from consumer electronics to automotive applications. Let's delve into the intricacies of molded plastic components, elucidating their multifaceted functionalities and the unparalleled value they bring to diverse sectors.
Introduction to Molded Plastic Components
Molded plastic components, fabricated through injection molding processes, epitomize durability and reliability in modern manufacturing. This production method entails injecting molten plastic material into a meticulously crafted mold cavity, allowing it to solidify and adopt the desired shape. The resultant components boast uniformity, intricate detailing, and exceptional strength, making them indispensable across a spectrum of industries.
Structural Integrity and Longevity
One of the primary attributes distinguishing molded plastic components is their structural integrity. Engineered to withstand diverse environmental conditions and mechanical stresses, these components exhibit good resilience, ensuring prolonged service life without compromising performance. Whether subjected to extreme temperatures, corrosive agents, or high-impact forces, molded plastic parts maintain their structural integrity, thereby bolstering the overall reliability of the products they adorn.
Functionality Across Industries
From automotive assemblies to medical devices, molded plastic components find widespread application in diverse sectors, each relying on their unique attributes to augment product functionality. In the automotive realm, these components contribute to lightweighting initiatives, enhancing fuel efficiency and reducing emissions. Moreover, their corrosion resistance and thermal stability render them ideal for under-the-hood applications, where exposure to harsh operating conditions is commonplace.
In the realm of consumer electronics, molded plastic components facilitate sleek and ergonomic designs, accommodating intricate circuitry and ensuring seamless integration with other system elements. Furthermore, their electrical insulating properties mitigate the risk of short circuits and electrical hazards, underscoring their significance in ensuring user safety and product reliability.
Customization and Design Flexibility
One of the inherent advantages of molded plastic components lies in their design flexibility and customization capabilities. Manufacturers can tailor these components to meet specific dimensional requirements, incorporating intricate features and geometries to optimize performance. Whether crafting intricate enclosures for electronic devices or designing ergonomic handles for handheld tools, the versatility of molded plastic components enables designers to unleash their creativity while adhering to stringent functional specifications.
Cost-Efficiency and Mass Production
In addition to their inherent mechanical properties and design versatility, molded plastic components offer compelling cost advantages, particularly when produced in large volumes. The efficiency of injection molding processes enables rapid production cycles, minimizing lead times and facilitating economies of scale. Consequently, manufacturers can realize significant cost savings without compromising on quality, making molded plastic components an economically viable solution for mass-produced goods across various industries.
Conclusion
In conclusion, molded plastic components embody the epitome of durability, reliability, and versatility in modern manufacturing. Their innate resilience, coupled with design flexibility and cost-efficiency, renders them indispensable across a myriad of applications, ranging from automotive to consumer electronics. As industries continue to evolve, the role of molded plastic components in enhancing product performance and efficiency will undoubtedly remain paramount, underscoring their enduring relevance in the ever-changing landscape of manufacturing.
Search
Categories
- Art
- Causes
- Crafts
- Dance
- Drinks
- Film
- Fitness
- Food
- Games
- Gardening
- Health
- Home
- Literature
- Music
- Networking
- Other
- Party
- Religion
- Shopping
- Sports
- Theater
- Wellness
Read More
**Die besten Tipps, um Monopoly Go Sticker zu kaufen: Sticker kaufen und sammeln für das ultimative Spielerlebnis**
Die besten Tipps, um Monopoly Go Sticker zu kaufen: Sticker kaufen und sammeln für das...
Audiobooks Market Forecast: Size, Drivers, Trends, and Competition
Press Release
The global audiobooks market has seen significant growth in recent years, driven...
Acheter Crédits FC 25 : Guide Complet pour Maximiser Votre Expérience de Jeu
Acheter Crédits FC 25 : Guide Complet pour Maximiser Votre Expérience de Jeu...
Maximize Your Gameplay: How to Efficiently Top Up Oneiric Shards in Honkai Star Rail
Maximize Your Gameplay: How to Efficiently Top Up Oneiric Shards in Honkai Star Rail
In the...
Prezzi Giocatori FC 25: Scopri le Valutazioni e le Novità del Mercato
Prezzi Giocatori FC 25: Scopri le Valutazioni e le Novità del Mercato
Nel mondo del...
© 2025 Scenario.press - libera espressione
English
