Stricter Quality Control Measures in Pipette Filter Tips Manufacturing
Posted 2024-03-14 09:01:32
0
6K
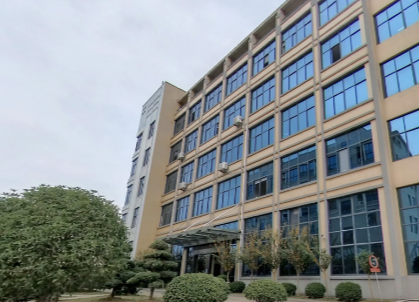
In the realm of laboratory research and experimentation, the reliability and accuracy of equipment are paramount. Among the essential tools for precise liquid handling, pipettes stand out as indispensable instruments. Integral to their functionality are the filter tips, ensuring contamination-free transfers and reproducible results. As the demand for high-quality filter tips surges, manufacturers face the challenge of meeting rigorous standards while maintaining efficiency and cost-effectiveness.
Pipette filter tips manufacturers are increasingly focusing on enhancing quality control measures throughout the production process. This concerted effort aims to deliver products that meet or exceed the exacting requirements of researchers and scientists worldwide. From raw material selection to final product testing, every stage is subject to stringent scrutiny to uphold the integrity of the filter tips.
At the outset, manufacturers carefully source materials known for their purity and compatibility with a wide range of solutions commonly handled in laboratories. High-grade plastics, such as polypropylene, are favored for their inertness and low leaching properties. By meticulously vetting suppliers and conducting thorough material analyses, manufacturers ensure the consistency and reliability of their inputs.
Once the raw materials are acquired, they undergo a series of precision manufacturing processes. Injection molding, a widely employed technique, enables the production of uniform filter tips with tight dimensional tolerances. Advanced machinery, operated by skilled technicians, ensures the reproducibility of each component. Throughout production, automated systems monitor critical parameters such as temperature and pressure to maintain good conditions and reduce variations.
Quality control protocols are integrated seamlessly into every step of the manufacturing workflow. In-process inspections are conducted regularly to detect any deviations from specifications promptly. Dimensional checks, visual inspections, and functional tests help identify and rectify issues before they escalate. By implementing robust quality checkpoints, manufacturers mitigate the risk of defects and ensure the consistency of their products.
The assembly stage is equally critical in maintaining product integrity. Filter tips must be securely affixed to the pipette, preventing leaks or detachment during use. Automated assembly equipment, calibrated to exacting standards, ensures precise alignment and proper attachment of components. Each assembled unit undergoes rigorous testing to verify its functionality and compatibility with various pipette models.
To validate the performance of their filter tips, manufacturers rely on a battery of tests conducted in controlled laboratory environments. These tests assess crucial parameters such as liquid retention, sealing integrity, and sample purity. By subjecting their products to simulated usage scenarios, manufacturers gain insights into their real-world performance and identify opportunities for optimization.
In response to the growing demand for sustainability, manufacturers are exploring eco-friendly alternatives and adopting greener practices. From utilizing recyclable materials to optimizing energy consumption, these initiatives aim to reduce the environmental footprint of filter tip production. By embracing sustainability as a core value, manufacturers align themselves with the broader societal trend towards responsible stewardship of resources.
In conclusion, the landscape of pipette filter tips manufacturing is characterized by a steadfast commitment to stringent quality control measures. Manufacturers recognize the pivotal role these components play in enabling precise and reproducible research outcomes. Through meticulous attention to detail, adherence to rigorous standards, and a relentless pursuit of excellence, they strive to meet the evolving needs of the scientific community. As research endeavors become increasingly complex and demanding, the reliability and performance of pipette filter tips remain paramount, driving continuous improvement and innovation in their manufacturing processes.
Search
Categories
- Art
- Causes
- Crafts
- Dance
- Drinks
- Film
- Fitness
- Food
- Games
- Gardening
- Health
- Home
- Literature
- Music
- Networking
- Other
- Party
- Religion
- Shopping
- Sports
- Theater
- Wellness
Read More
Come Accumulare FIFA Coins e Crediti FC25 per Massimizzare il Tuo Gioco in FC 25
Come Accumulare FIFA Coins e Crediti FC25 per Massimizzare il Tuo Gioco in FC 25
Se sei un...
**Titel: Alles über FC 25 Spieler kaufen: Preise und Angebote im Überblick**
Alles über FC 25 Spieler kaufen: Preise und Angebote im Überblick
Das Interesse an FC...
What Are the 6 Luckiest Numbers in Capricorn?
Capricorn is the tenth sign in the zodiac. It is ruled by Saturn. This planet brings discipline,...
Internal Heat Exchanger (IHX) Market: Enhancing Thermal Management Systems
The Internal Heat Exchanger market plays a pivotal role in advancing thermal management across...
Optimisez votre expérience de jeu avec le Recharge Honkai Star Rail : Guide complet pour porter votre aventure à un niveau supérieur !
Optimisez votre expérience de jeu avec le Recharge Honkai Star Rail
Dans l'univers...
© 2025 Scenario.press - libera espressione
English
