What Tolerances Can Be Achieved With CNC Milling Aluminum?
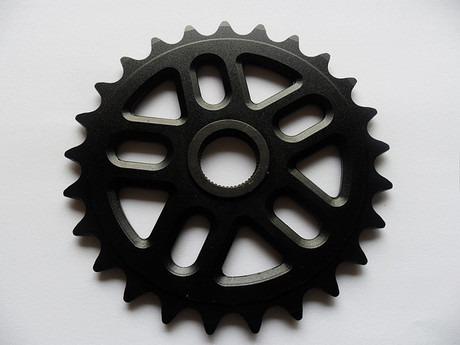
Tolerances for CNC milling aluminum are determined by several key factors, and understanding these factors is critical to ensuring your project receives the precision it requires. Here is a breakdown:
Factors Influencing Achievable Tolerances
l Machine Capabilities: Different CNC machines have varying degrees of precision. High-end, modern machines usually have tighter tolerances than older or basic models. 5-axis machines generally have tighter tolerances than 3-axis machines.
l Tooling Selection: The size and type of cutting tools have a significant impact on the achievable tolerances. Smaller tools allow for greater precision but may not be appropriate for roughing operations. The tool's sharpness and condition are also important considerations.
l Desired Finish: Roughing operations have wider tolerances than finish machining, which aims for smooth surfaces. Balancing surface finish with the desired precision is critical.
l Material Properties: Aluminum alloys differ in terms of hardness and machinability. Softer alloys, such as 6061, can accommodate tighter tolerances than harder alloys, such as 7075.
l Part Geometry: Simple, straight-line shapes are easier to mill to tight tolerances than complex, curved features. Undercuts, thin walls, and sharp corners may necessitate looser tolerances.
l Production Volume: High-volume production often prioritizes speed and may use looser tolerances, whereas individual prototypes or low-volume parts may require tighter tolerances for precise fit.
General Tolerance Ranges
l Typical Range: ±0.001" to ±0.005" (0.03 mm to 0.13 mm) is a common range for CNC milling aluminum.
l High-Precision Machines: Some advanced machines can achieve ±0.0005" (0.013 mm) or even better in ideal conditions.
l Complex Geometries or Large Parts: Tolerances might be wider, up to ±0.010" (0.25 mm) or more, depending on the level of complexity and size.
In your CNC machining drawings, specify the tolerances you require. Discuss the acceptable tolerances with your preferred manufacturer based on their machines, tooling, and experience. Consider the trade-off between tighter tolerances and increased costs and production times. Not every part requires extremely tight tolerances; prioritize them based on functionality and critical dimensions. If you want to learn more about CNC milling aluminum, such as alloy and tooling selection, please contact a qualified CNC machining expert. They will help you ensure that your aluminum parts meet the tolerances required for optimal performance and functionality.
- Art
- Causes
- Crafts
- Dance
- Drinks
- Film
- Fitness
- Food
- Игры
- Gardening
- Health
- Главная
- Literature
- Music
- Networking
- Другое
- Party
- Religion
- Shopping
- Sports
- Theater
- Wellness
