A Customer's Guide to Injection Molding Machine Control Systems
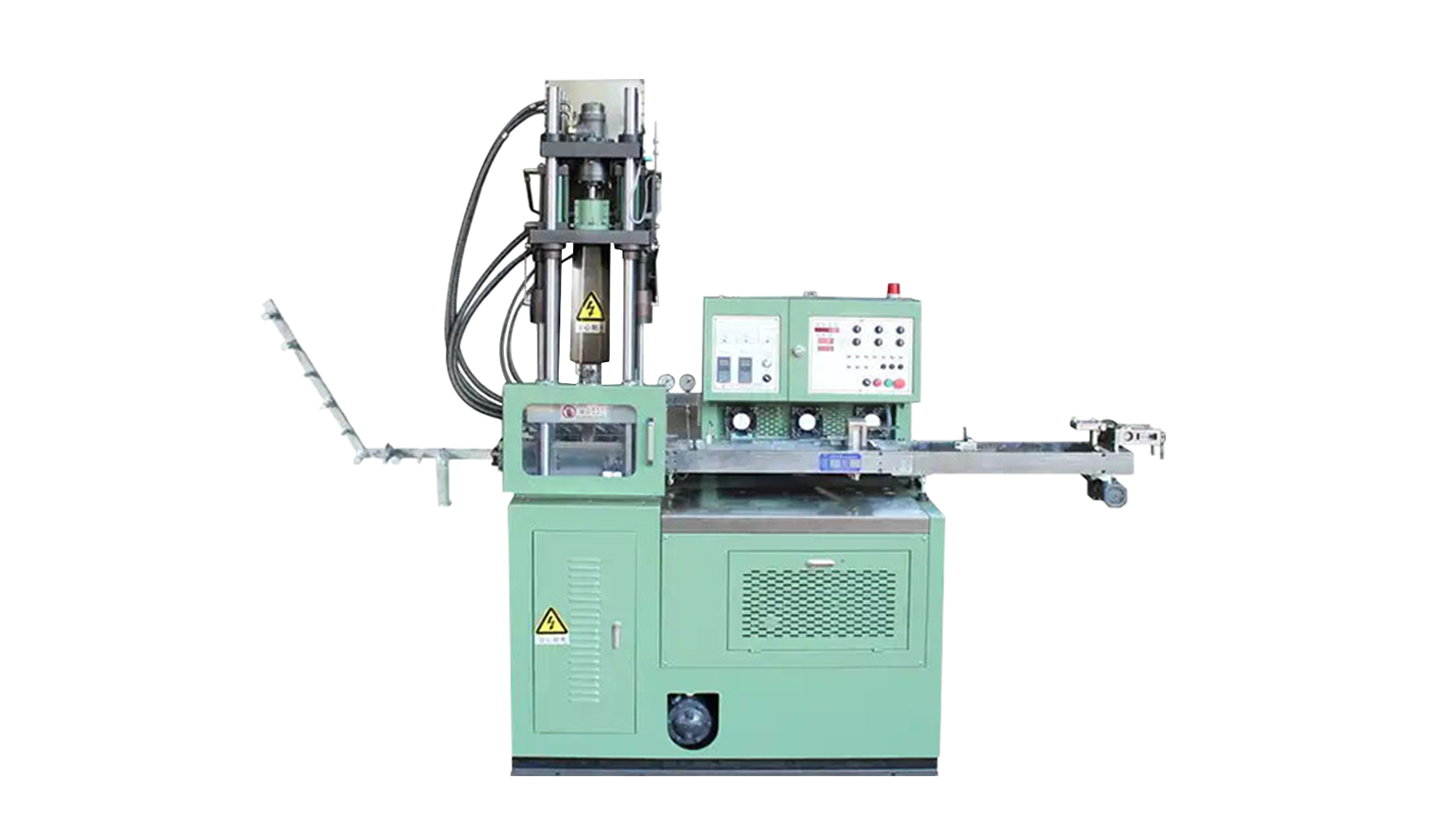
In the intricate world of manufacturing, the role of injection molding machines is paramount, and at the heart of their functionality lies the often-overlooked hero—the injection molding machine control system. This customer-centric exploration aims to demystify the complexities surrounding these control systems, shedding light on their significance, functionalities, and the impact they have on enhancing the injection molding process.
Understanding the Foundation: What Is an Injection Molding Machine Control System?
Before delving into the customer's perspective, it's crucial to comprehend the foundational aspects of an injection molding machine control system. This system serves as the brain of the injection molding machine, orchestrating and regulating various processes to ensure the precise and efficient production of molded components.
Customer-Focused Advantages of Injection Molding Machine Control Systems:
Now, let's unravel the benefits that customers can anticipate when incorporating advanced injection molding machine control systems into their manufacturing processes.
Enhanced Precision and Control:
Microscopic Regulation
Injection molding machine control systems enable customers to achieve unprecedented levels of precision and control. The ability to regulate variables at a microscopic level ensures that each molded component meets exact specifications, contributing to overall product quality.
Optimized Production Efficiency:
Real-Time Monitoring and Adjustment
The real-time monitoring capabilities of control systems empower customers to optimize production efficiency. Any deviations from the set parameters can be identified and adjusted promptly, minimizing downtime and maximizing throughput.
Intuitive User Interface:
User-Friendly Controls
Modern injection molding machine control systems feature intuitive user interfaces, enhancing the user experience. Customers can navigate through settings, monitor processes, and make adjustments with ease, reducing the learning curve for operators.
Versatility in Material Processing:
Adaptability to Varied Materials
Customers appreciate the adaptability of injection molding machine control systems to a wide range of materials. From traditional plastics to advanced polymers, these systems can be fine-tuned to accommodate diverse materials, expanding the possibilities for component manufacturing.
Energy-Efficient Operation:
Smart Energy Management
Many contemporary control systems are equipped with energy-efficient features. Customers benefit from optimized energy usage, contributing to cost savings and aligning with sustainability goals.
High-Speed Operation:
Swift and Precise Cycle Times
The speed at which injection molding machines operate is a critical factor for customers. Control systems facilitate high-speed cycles, ensuring swift and precise molding processes, which is particularly advantageous for high-volume production.
Quality Assurance:
Built-In Quality Checks
Injection molding machine control systems often incorporate built-in quality checks. Customers can rely on these systems to monitor and ensure the consistency and quality of each molded part, reducing the likelihood of defects.
Remote Monitoring and Troubleshooting:
Connectivity for Remote Access
The ability to remotely monitor and troubleshoot injection molding processes adds a layer of convenience for customers. This feature facilitates proactive maintenance, minimizing the impact of potential issues on production schedules.
Real-World Perspectives: Testimonials from Manufacturers
To provide a tangible understanding of the customer's perspective, let's explore a few testimonials from manufacturers who have embraced advanced injection molding machine control systems.
Jessica Reynolds, Plastics Industry Veteran:
"The injection molding machine control system has truly revolutionized our operations. The level of precision we can achieve is unmatched, and the intuitive controls make the entire process more accessible. It's like having an extra set of expert hands overseeing every aspect of production."
Daniel Chang, Medical Device Manufacturer:
"In the medical industry, quality is non-negotiable. The injection molding machine control system has become our ally in ensuring that each component meets the stringent standards required for medical devices. The real-time monitoring is a game-changer for maintaining consistency."
Emily Hernandez, Consumer Electronics Producer:
"Time-to-market is crucial in the electronics industry. The high-speed operation of our injection molding machines, coupled with the control system's adaptability to different materials, gives us a competitive edge. It's not just about speed; it's about speed with precision."
Conclusion: Elevating Injection Molding with Advanced Control Systems
In conclusion, the injection molding machine control system emerges as a silent orchestrator, playing a pivotal role in shaping the customer's manufacturing journey. As industries evolve and demand higher levels of precision, efficiency, and adaptability, these control systems stand as indispensable components in the injection molding landscape. Customers navigating the intricate world of manufacturing can rely on these systems not just as regulators but as partners in achieving excellence in molded component production.
From user-friendly interfaces to real-time monitoring, the injection molding machine control system is designed to enhance the overall injection molding experience. As customers seek solutions that streamline operations, ensure quality, and provide adaptability to changing production needs, these control systems emerge as indispensable assets. The injection molding machine control system is not just a technological component; it's a catalyst for efficiency, precision, and customer satisfaction in the dynamic realm of injection molding.
- Art
- Causes
- Crafts
- Dance
- Drinks
- Film
- Fitness
- Food
- Games
- Gardening
- Health
- Home
- Literature
- Music
- Networking
- Other
- Party
- Religion
- Shopping
- Sports
- Theater
- Wellness
