Evaluating Surface Finish Consistency of Non-Woven Fiber Wheel in Wet vs. Dry Grinding
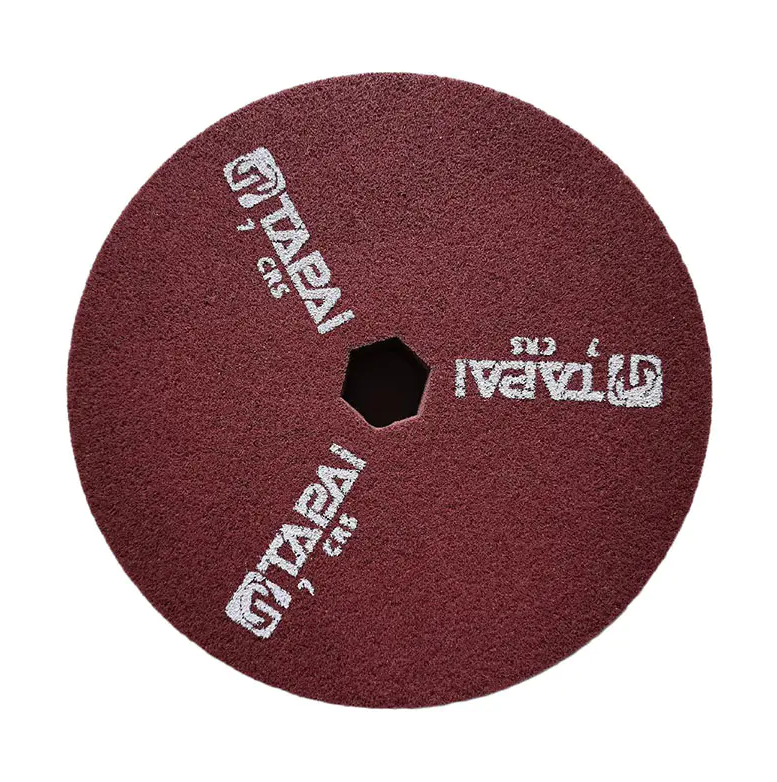
In surface conditioning processes, both dry and wet grinding methods are commonly employed depending on the application, material, and desired surface finish. The choice between the two can significantly affect heat generation, abrasive performance, and the longevity of the tool used. When it comes to the Non-Woven Fiber Wheel, an abrasive tool widely known for its consistent surface treatment capabilities, flexibility, and ability to produce uniform finishes, users often ask: Does it perform equally well under both dry and wet grinding conditions?
The Non-Woven Fiber Wheel is made from a network of synthetic fibers impregnated with abrasive grains and bonded together using resin systems. This structure is open and porous, which naturally reduces heat buildup and allows for dust and swarf to be expelled during use. As such, in dry grinding, these wheels often perform better than traditional coated abrasives or grinding wheels in terms of temperature management and finish consistency. The open design prevents clogging, allowing longer usage without glazing or burning the workpiece surface.
However, wet grinding introduces a coolant or lubricant—usually water-based or oil-based—which drastically changes the dynamics of the grinding process. The liquid acts as a cooling agent, reducing the temperature at the contact point between the wheel and the workpiece. This has the immediate benefit of extending the life of the Non-Woven Fiber Wheel, especially in heavy-duty or high-speed operations. It also helps in achieving finer finishes by washing away debris and minimizing surface loading.
In terms of actual performance, the Non-Woven Fiber Wheel generally performs better in wet grinding for several reasons. First, the presence of fluid minimizes friction and heat, which in turn reduces the degradation rate of both the abrasive grains and the bonding resin. Second, the surface of the workpiece remains cleaner during the operation, as the fluid helps remove micro-particles that would otherwise embed into the wheel or the material being worked on. This results in a smoother and more uniform finish, especially on sensitive materials such as stainless steel, aluminum, and non-ferrous alloys.
That said, dry grinding still offers advantages in specific scenarios. For field work, where coolant systems are unavailable, or when working on materials that react poorly to moisture (such as certain composites or electrical components), dry grinding with a Non-Woven Fiber Wheel can deliver reliable results. The wheel’s inherent ability to dissipate heat and resist clogging makes it one of the more forgiving options for dry applications.
It’s important to note that not all Non-Woven Fiber Wheels are designed for wet environments. Some wheels use bonding agents that may degrade or swell when exposed to fluid over time. Therefore, when selecting a wheel for wet grinding, it’s essential to confirm its compatibility with the coolant and operating conditions.
In conclusion, while the Non-Woven Fiber Wheel performs admirably in both dry and wet grinding conditions, it generally achieves better results and longer life when used in wet environments, provided the wheel is specifically rated for such use. Wet grinding enhances cooling, reduces friction, and improves surface finish quality. However, the wheel’s natural properties still allow it to function effectively in dry conditions, making it a versatile and reliable option for a wide range of finishing and deburring tasks.、
Non-Woven Fiber Wheel is a specialized industrial tool designed for precision surface preparation, polishing, and material removal tasks. Made from a blend of non-woven fibers and high-quality abrasives, these wheels are crafted to withstand elevated temperatures and harsh operating conditions.
- Art
- Causes
- Crafts
- Dance
- Drinks
- Film
- Fitness
- Food
- Games
- Gardening
- Health
- Home
- Literature
- Music
- Networking
- Other
- Party
- Religion
- Shopping
- Sports
- Theater
- Wellness
