Manufacturing Insights into the Lithium-Ion Angle Grinder
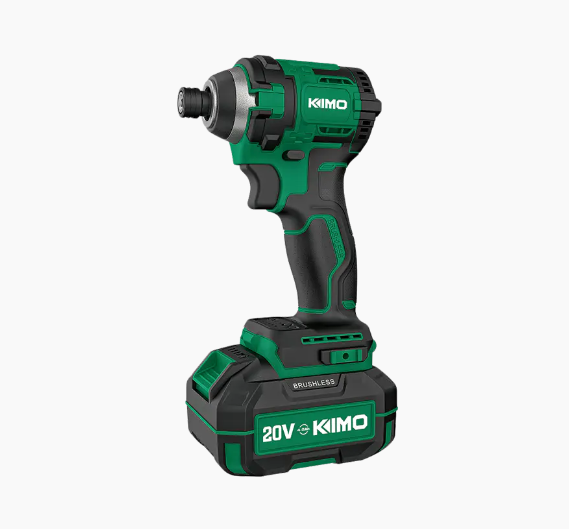
The Lithium-Ion Angle Grinder has gained traction in various industries due to its cordless design and convenience. From a manufacturing standpoint, producing a reliable and efficient Lithium-Ion Angle Grinder involves a complex process that integrates multiple disciplines, including mechanical engineering, battery technology, and quality control.
One of the central components in the manufacture of a Lithium-Ion Angle Grinder is the battery system. Lithium-ion batteries are selected because of their favorable energy density and relatively lightweight. The manufacturing process for these batteries requires careful attention to safety, as improper handling or defects can lead to hazards such as overheating or short circuits. Factories producing the batteries for Lithium-Ion Angle Grinders must implement strict quality assurance protocols and use precise assembly techniques to ensure product reliability.
The motor assembly is another critical element in the Lithium-Ion Angle Grinder. Many manufacturers opt for brushless motors to improve durability and efficiency. Producing these motors involves detailed winding of copper coils, precise placement of magnets, and thorough testing of each unit's electrical properties. The motor's performance directly influences the grinder's ability to maintain steady speed and torque during demanding tasks, so manufacturing consistency is vital.
The housing and structural design of the Lithium-Ion Angle Grinder also require attention. Materials such as reinforced plastics or lightweight metals are often used to balance durability and weight. Injection molding is commonly used to create ergonomic grips and guards, allowing for comfortable and safe handling. During manufacturing, maintaining tight tolerances in these parts helps ensure that components fit correctly and that the tool functions smoothly.
Assembly lines for the Lithium-Ion Angle Grinder often combine manual and automated steps. While robots can assist with tasks like battery insertion or screw fastening, human oversight remains important for quality checks and adjustments. This hybrid approach allows manufacturers to manage production costs while maintaining acceptable product quality.
Thermal management is another aspect considered during manufacturing. Since the Lithium-Ion Angle Grinder operates at high speeds and can generate heat, manufacturers often incorporate ventilation features or heat sinks to dissipate warmth. Ensuring effective thermal control contributes to the longevity and safety of the tool.
In addition to mechanical assembly, electronics integration is essential in the production of the Lithium-Ion Angle Grinder. Components like speed controllers, sensors, and safety switches are installed and calibrated to coordinate the grinder's operation. The manufacturing process must ensure that these electronic parts are shielded from dust and vibrations common during grinding tasks.
Testing is a critical phase before the Lithium-Ion Angle Grinder reaches the market. Each unit typically undergoes performance tests that simulate real-world usage, checking parameters such as battery life, motor speed, and safety functions. This stage helps identify defects early and reduces the chance of failures after purchase.
Sustainability has also influenced manufacturing choices for the Lithium-Ion Angle Grinder. Some producers aim to use recyclable materials or implement processes that reduce waste. This trend reflects growing interest in environmental responsibility within the power tool industry.
The manufacturing of the Lithium-Ion Angle Grinder requires coordination among multiple suppliers, including those for batteries, motors, electronics, and casings. Managing this supply chain efficiently impacts production schedules and final product availability.
The production of the Lithium-Ion Angle Grinder combines advanced battery technology, precision motor manufacturing, and thoughtful design to meet user demands. By focusing on quality control, safety, and efficiency during manufacturing, companies aim to deliver tools that perform consistently across a variety of applications. The integration of electronics and mechanical parts in a streamlined process supports the practical features that make the Lithium-Ion Angle Grinder a valuable tool in today's market.
- Art
- Causes
- Crafts
- Dance
- Drinks
- Film
- Fitness
- Food
- Παιχνίδια
- Gardening
- Health
- Κεντρική Σελίδα
- Literature
- Music
- Networking
- άλλο
- Party
- Religion
- Shopping
- Sports
- Theater
- Wellness
