Difference Between Weld Neck Flanges and Slip-On Flanges
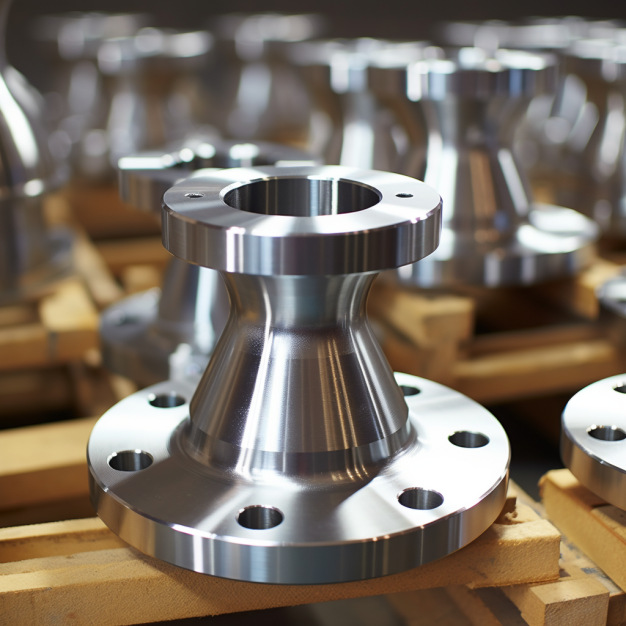
Weld neck flanges and slip-on flanges are two common types of flange connections used to join piping systems. While both allow for bolted joining of pipes, they differ significantly in their design and installation methods. A thorough understanding of the key distinctions between weld neck and slip-on flanges is important for specifying the right flange type for an application.
Weld Neck Flange Design
As the name implies, weld neck flanges feature an extended tubular “neck” that is welded to the end of a pipe. This creates a full-strength circumferential welded joint between the pipe and flange. Weld neck flanges conform to standards like ASME B16.5 and typically have welding ends that match standard pipe schedules or diameters.
Key advantages of weld neck flanges include their robust welded connection providing full-rated pipe wall thickness and pressure capabilities up to the flange. They can withstand high internal pressures and loads. The welded joint also prevents leakage at the pipe-to-flange interface.
Slip-On Flange Design
Unlike weld neck flanges, slip-on flanges do not require welding. They are designed to be slipped over the end of a pipe and bolted in place. An elastometric gasket creates the seal between the pipe outer diameter and the flange mating surface.
While not requiring welding, slip-on flanges provide less structural strength compared to a weld neck joint since they rely on compression of the gasket rather than a welded connection. They are best suited for lower pressure applications under 150 PSIG.
Installation Methods
The installation of weld neck and slip-on flanges differs significantly due to their unique designs:
Weld neck flanges require pipe preparation including chamfering and welding according to codes like ASME Section IX. |
Slip-on flanges simply slide over a pipe end and can be bolted together without any welding. |
This makes slip-on flanges faster to install in the field, while weld neck flanges involve more pre-installation steps like pipe fitting and qualification of welding procedures.
Standards Compliance
Recognized standards cover both weld neck and slip-on flange designs. Key differences include:
- ASME B16.5 specifies dimensional requirements for weld neck flanges in various pressure classes up to 2500 PSIG.
- MSS SP-44 covers dimensions of slip-on flanges for use with standard weight pipe in lower pressure systems.
Proper specification per relevant piping codes ensures each flange type can perform reliably within its rated pressure range.
Applications
Based on their design strengths and assembly methods, weld neck and slip-on flanges excel in different piping applications:
- Weld neck flanges commonly used in high pressure systems like refineries, power plants, oil/gas pipelines.
- Slip-on flanges well-suited for lower pressure applications in buildings (air, water, steam, natural gas).
Considering installation complexity and structural needs guides selections of weld neck versus slip-on flange connections for a given process system.
- Art
- Causes
- Crafts
- Dance
- Drinks
- Film
- Fitness
- Food
- Games
- Gardening
- Health
- Home
- Literature
- Music
- Networking
- Other
- Party
- Religion
- Shopping
- Sports
- Theater
- Wellness
