A wide variety of lathe cutting tools are available for use with CNC lathe machines and for a variety of purposes
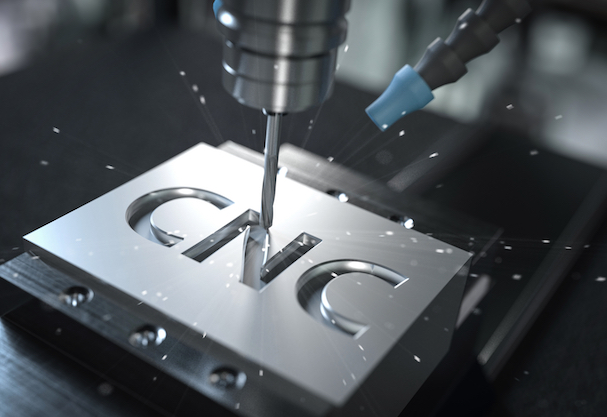
Therefore, these lathe tools are versatile enough to be utilized for a wide range of applications. It is able to perform the function of shaping materials such as metals and wood materials by utilizing a mechanism that is capable of holding and rotating the material. This allows it to perform the function of shaping materials. Turret lathes, on the other hand, are an excellent option for carrying out high-volume production because they are ideally suited for having the capability to make rapid tool changes. The bed is the component that is comprised of the base of the lathe. In addition to being the component to which all of the cutting tools for the lathe are attached, the bed is also the component that also supports the lathe.
There are a number of different lathe cutting tools that fall under the fundamental categories of lathe tools. To begin, there are the fundamental categories of lathe tools. This is due to the fact that it is significant to have an understanding of what a lathe die casting machine is.
Blade-turning tools and equipment
There are many different instruments that are utilized.
Similar to the construction of a conventional face milling tool, which is distinguished by a cutting edge that is located on the side of the tool, the construction of a lathe facing tool is comparable to that of a conventional face milling tool. The tools that fall into these two categories are referred to as right-hand facing tools and left-hand facing tools individually.
Instruments that require a lot of effort: In addition to the standard boring bar that is found on these tools, carbide boring tools also come with a cutting tool that is attached to the end of the tool.
For example, single-point boring bars only have a single cutting edge, whereas multi-point boring bars have multiple cutting edges. This is the primary distinction between the two types of boring bars.
By utilizing a tool that only has one angle, it is possible to create a chamfer that maintains the same angle throughout the entire length of the cut. This is something that is possible.
It is possible to increase the flexibility of the chamfering process by using indexable chamfering tools that have inserts that can be replaced.
- Additionally, chamfering can be accomplished with turning lathe tools by positioning the lathe in such a way that it is at an angle that is right angle to the workpiece
- This will allow the lathe to have a right angle to the workpiece
- When it comes to thread cutting tools, there are two distinct categories that can be found: internal thread cutting tools and external thread cutting tools
It is the external thread-cutting tool that is responsible for this task, and it is responsible for producing the threads that are applied to the surface of the workpiece. Smoothing out rough edges is the purpose of this particular type of tool. Knurling tools come in a variety of shapes and sizes, the most common of which are straight knurling tools and diagonal knurling tools simultaneously.
When knurling tools are used, it is possible to create a raised pattern on the surface of a workpiece. This raised pattern can also improve the aesthetics of the workpiece. Not only is their production more precise and effective, but they also have individualized profiles that can be adapted to fit a variety of shapes. Because of this, picking them is a more appealing choice. These tools have the capability of either decreasing or increasing the diameter of a workpiece, depending on the individual's selection of the desired effect. This enables them to fulfill the requirements that are associated with the workpiece. The tools that are in the shape of a V and those that cut squares are the most common types of tools that are offered by lathe die casting machines. In the process of manufacturing a wide variety of lathe tools, the following are some examples of materials that are frequently utilized in the factory:
components for the lathe that were fabricated from steel and cutters as well
The steel that is able to move at a quick pace
The cutting tools for lathes that are made from high-speed steel are hard in addition to being extremely durable and resistant to wear. In addition, they are extremely durable.
Lathing operations that are performed at a moderate speed, such as rough and semi-finish machining, make extensive use of high-speed steel (HSS) tools. On the other hand, they are not suitable for high-speed machining, and they require a greater number of tool changes while they are being used. Additionally, they require these changes to be made more frequently.
- Art
- Causes
- Crafts
- Dance
- Drinks
- Film
- Fitness
- Food
- الألعاب
- Gardening
- Health
- الرئيسية
- Literature
- Music
- Networking
- أخرى
- Party
- Religion
- Shopping
- Sports
- Theater
- Wellness